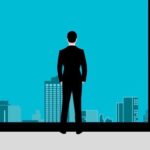
生産技術の生産準備ってつらいの?
具体的な仕事内容は?
知りたいけど一体誰に聞けばいいんだ…
そんな悩みに
大手自動車部品メーカー2社の生産技術/生産準備チームで
キャリアを積んでいる私が答えます。
- 生産技術/生産準備業務の一連の流れ
- 生産技術/生産準備業務の具体的な内容
- 生産技術/生産準備業務のやりがい・つらさ
生産技術の生産準備と聞くと
言葉の通り
製品の生産の準備をするということは
なんとなく想像できますが…
具体的な仕事内容までは分からないですよね。
私も生産準備チームへ配属を言い渡された時は
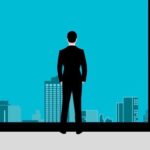
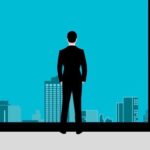
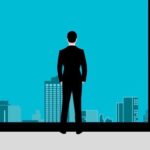
生産技術部の生産準備チームに配属?
…一体どんな仕事なの?(笑)
と気になって
生産準備の仕事内容について
ネットで調べていた思い出があります。
今回は
生産技術の生産準備業務に興味がある人へ向けて
現役で生産準備業務を行っている私が
経験を踏まえて解説していきます。
本記事は
生産準備業務の理解を深めたい人にとって
大変参考になる興味深い内容になっていると思います。
※経験を踏まえた個人的見解が含まれる点はご了承ください
それではさっそくみていきましょう。
生産技術の生産準備はつらい?具体的な仕事内容は?現役生産技術員が解説
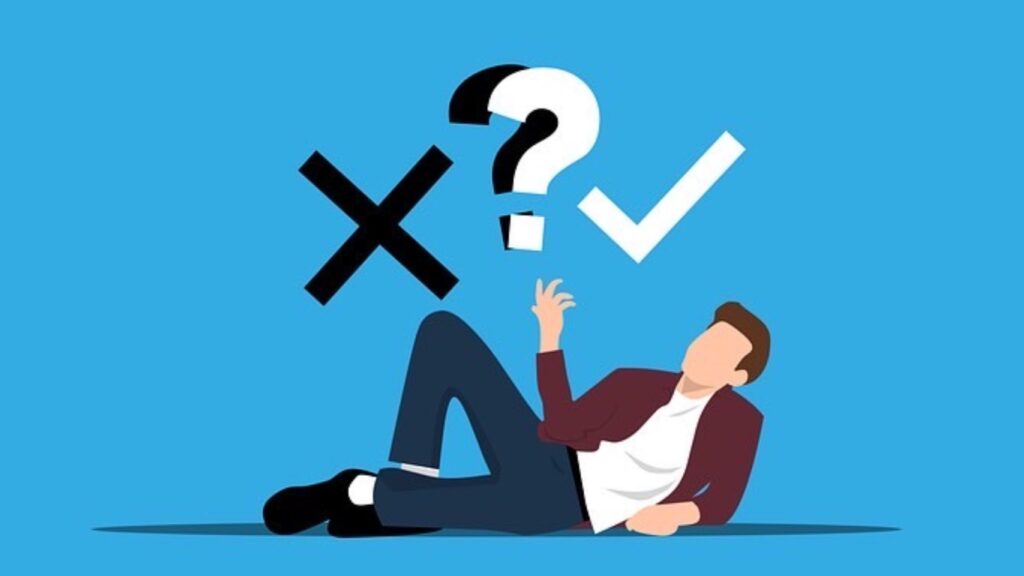
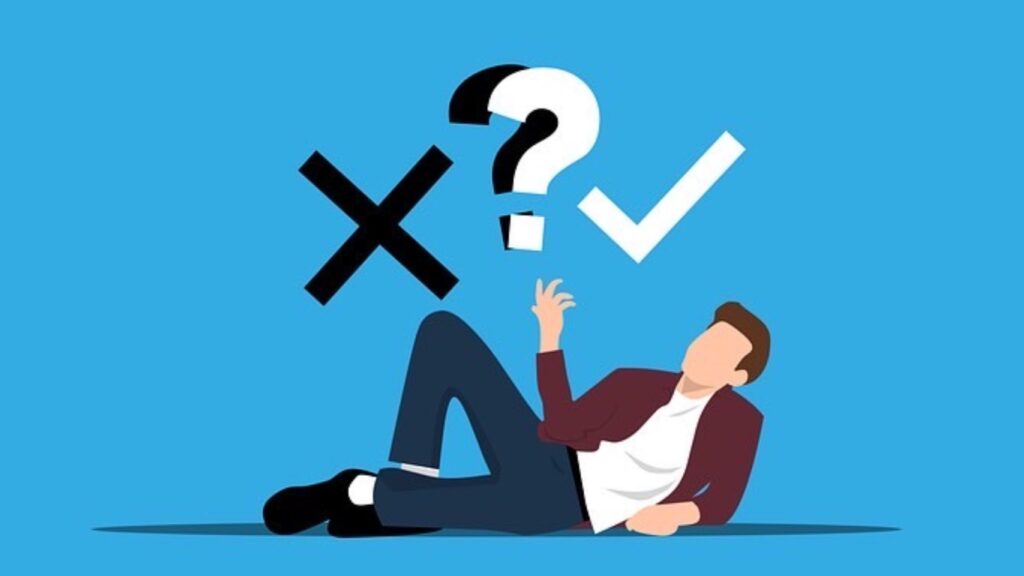
生産技術/生産準備の主な業務は
製品を生産する準備をすることです。
そして忙しくて大変です(笑)
一言では簡単に伝わらないので
詳しく解説していきます。
お客さんの要望する製品を期日までに生産できるように
工程整備を行うことが主な業務になります。
他にも製品の生産ライン変更の検討や
工程改善も生産準備の業務です。
部署の人気で言ったらどうでしょう…
低い方かなと…(笑)
希望していないのに
配属される人が多い部署になると思います(私もそう)
ですが
いざやってみると自分に合っているかもしれませんよ。
やりがいに関しては保証します(笑)
製品が立ち上がるまでのステップをざっくり記載すると
① 見積図入手(営業)
② 製品の検討
③ 検討トライ
④ ライン立上げ/改造
⑤ 条件出し
⑥ 品質確認
⑦ 標準類作成
⑧ 初品
⑨ 量産
になります。
これだけで大変な部署だって分かりますよね…(笑)
各ステップでの業務を詳しく見ていきましょう。
製品の検討
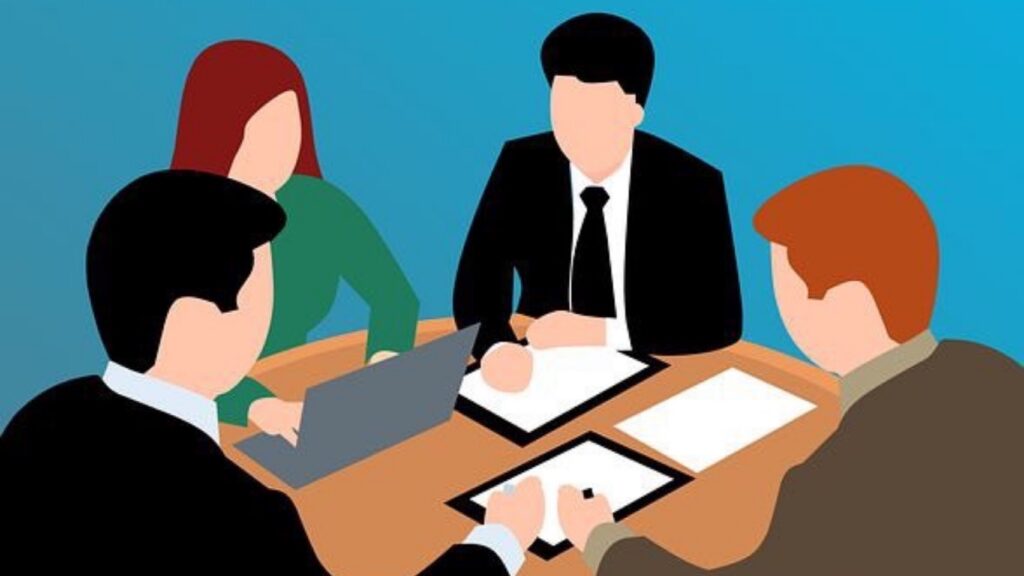
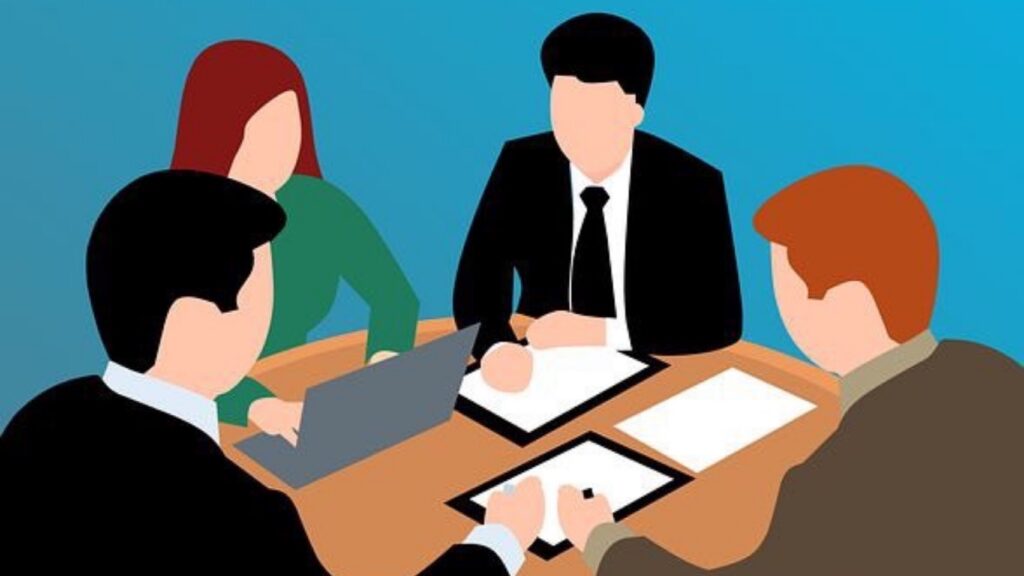
見積図を確認しながら社内で実現可能かどうか
(受注を目指すか)を検討します。
営業、生産管理、製造、品質保証、検査などと一緒に
コストや納期、生産実現性などから
受注の良否判断や実現性について話し合います。
1回の検討会では決定できず数回行う場合が多いです。
検討会の実施回数は特に決まっておらず
結論が出るまで行います。
但し、お客さんへの回答納期は厳守です。
各部署で懸念点をトライで確認しながら
検討会とトライを繰り返して受注する/しないの結論を出します。
このとき注意しないといけないのが
「できると言ってしまったらやるしかない」という点です。
お客さんに「できる」と回答した時点で
正式な発注(契約)となります。
後から検討不足で
できませんでしたは通りません。
お客さんの生産計画にも大きな損失を与えてしまい
賠償金の支払いなど大きな問題に発展することもあります。
この検討段階での生産技術/生産準備のトライ結果は受注の有無に大きく関わる重要なステップです。
まだ検討の段階だと確認を曖昧に行い
不確かな情報のみで
できる/できない回答すると
取り返しのつかいことになり
後ほど自分が苦しくなるので要注意です(経験者です…)
検討の段階からすでに大きな責任があることを自覚して取り組みましょう。
納期も同様で
確実に対応可能な日程で受注を目指しましょう。
「製品の検討」でつらいこと
- 会社としては受注を取りたいので検討の段階で
生産が困難な条件でも生産技術部で
何とか生産できるようにしてくれと他部署から言われる - 参加する関連部署が多くて話がまとまりずらくなる
- 立場が強い(発言力がある)人がいる部署の
意見が通りやすくなってしまう
検討トライ
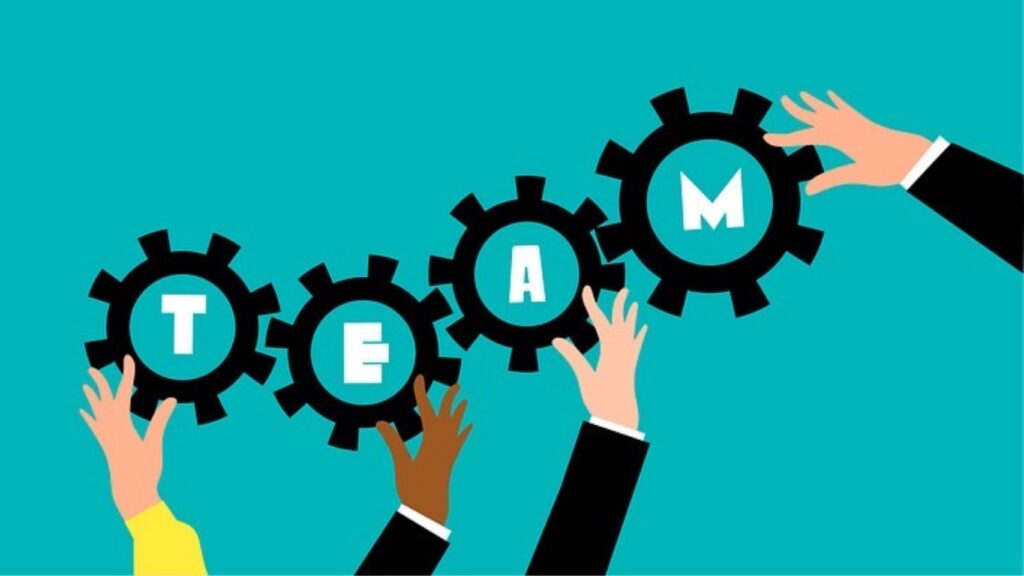
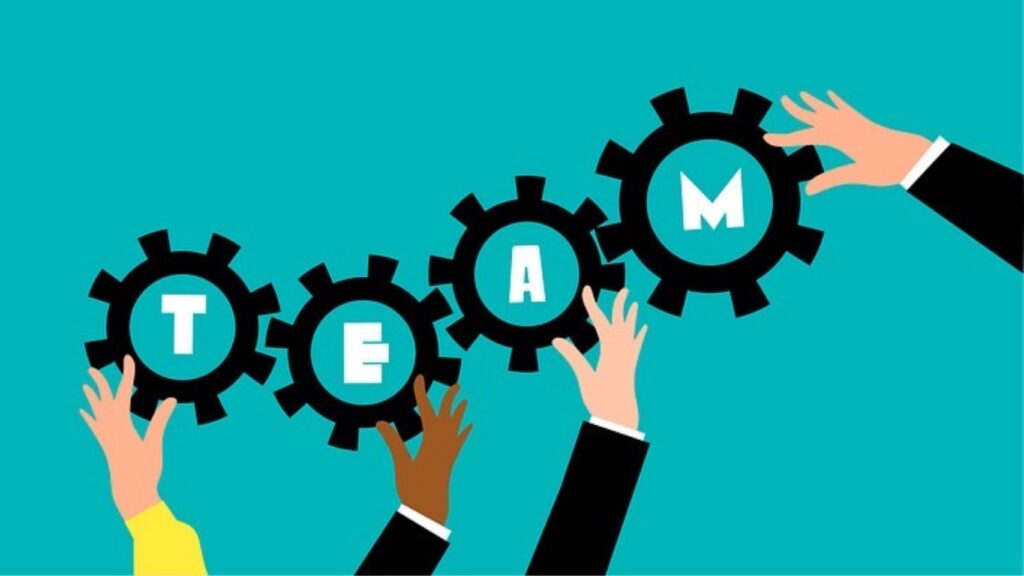
検討トライについて
具体的にどんなことを確認するのか見ていきます。
検討会で挙げられた生産技術部としての確認すべき懸念点が
実現可能か確認します。
生産の確認
例えば
新製品をお客さんから入手→既設の量産ラインで流動可能か確認します。
※既設ラインでそのまま流動可能な場合は生産技術としてやるべき業務が軽減されるラッキーなパターンです
→流動可能であれば採算次第で受注
→流動不可であれば新ラインの立上げもしくは
既設ラインの改造を検討
※ラインの新設or既設の改造どちらで対応するかは製品の生産数にも左右されます
少量生産品のためにわざわざ新ラインを立上げるのは採算性が怪しくなります。
また
量産のラインの設備を使用(借用)して検証を実施する時は検証後に必ず検証前の状態に戻すこと。
これを忘れると大量の不良を発生させてしまう要因にもなりますので注意が必要です。
品質の確認
顧客からの
要求規格の満足及び測定が可能かどうかの確認する
→要求規格の実現が不可であれば公差緩和の打診
→測定不可であれば可能な条件(測定基準の変更)の打診
要求の規格を満たせるかどうかに関しては
社内の技術力も〇/✕判定に大きく関わります。
測定不可とはどんな場合があるのかというと
- そもそも要求項目を測定できる検査機を所持していない(受注に合わせて検査機の購入で対応の場合あり)
- 図面指示の基準面がばらつく
(基準となる面が図面通りでないと測定不可)
→バリなどが発生してしまい基準がばらついてしまう
などです。
懸念点に関しては
量産にある類似製品や過去のトライ結果などを参考にして確認しましょう。
同じミスを犯さないことが重要です。
「検討トライ」でつらいこと
- 量産ラインでの確認が必要なため休日出勤が多くなる
- 製品によっては複雑な図面の読解能力が必要
- 測定に関しては検査グループでしか扱えない
検査機もあり日程を合わせて協力依頼が必要
ライン立上げ/改造
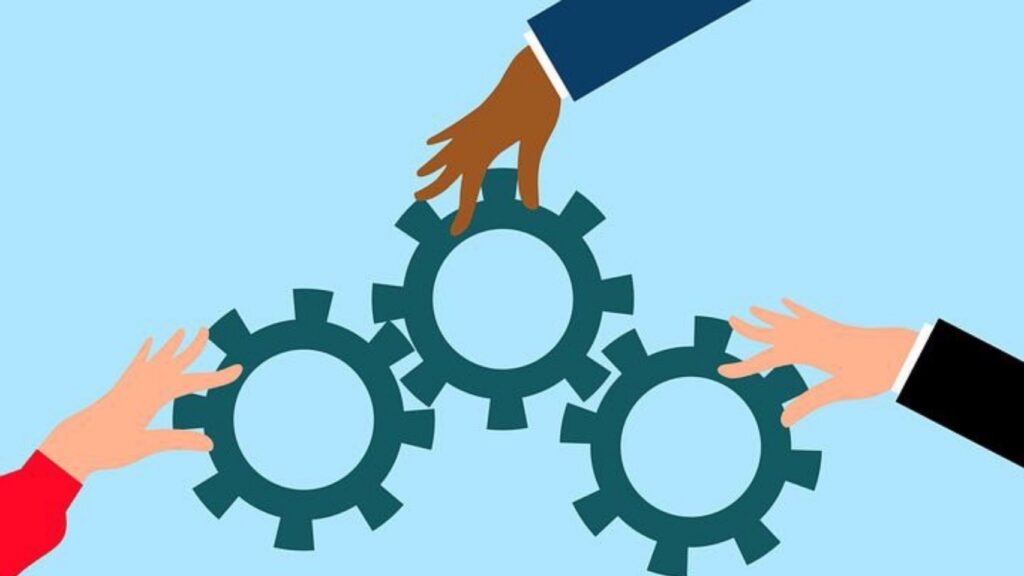
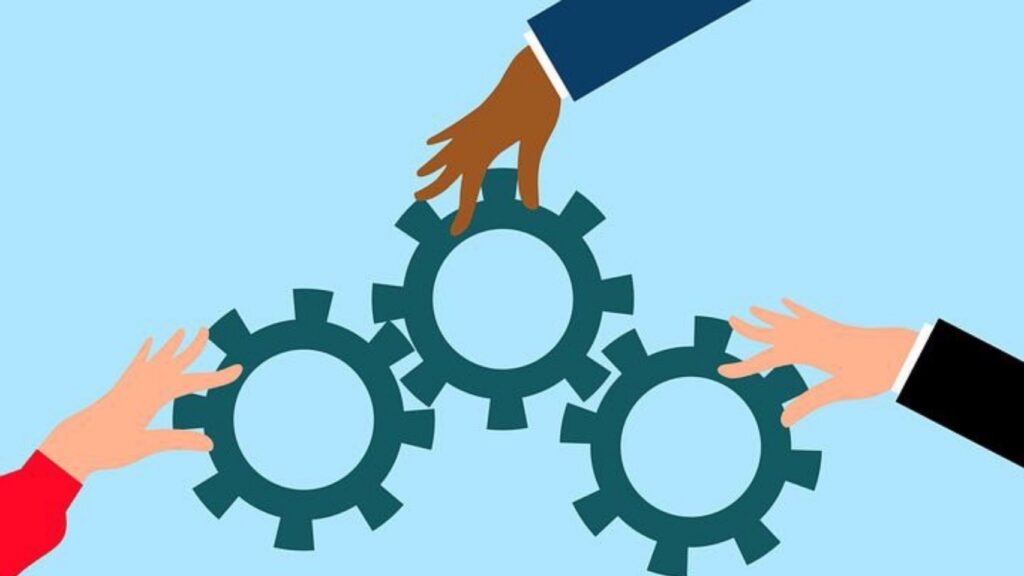
ライン立上げであれば設備の検討・導入が必要です。
このとき
設備仕様の検討を行いますが
生産技術部として
安全で生産性の高い設備の導入を心掛けましょう。
安全は何よりも優先されます。利益/納期よりも安全です。
生産技術部は
安全第一の設備を導入する責任がある。
安全<利益
利益<安全
働く側として
どっちの会社で働きたいか言わずとも分かるはずです。
生産技術部として
設備を導入する際は仲間の社員を守るためにも
安全は何よりも優先ということを徹底してください。
安全は何よりも優先
また
設備の配置(レイアウト)検討も業務のひとつで
作業者に無駄な動きがないレイアウトの検討が必要です。
災害時の安全通路の確保も忘れてはいけません。
品質に関しては
作業者の
「ミスが起こってから流出を防ぐ」ではなく「ミスが起こらない」仕組み
を導入した設備検討ができると◎です
例えば
・品番ごとに異なる金型治具のセットミスが懸念
→切り欠きなどを追加して物理的に品番と整合が取れている
治具でないとセットできないような仕組み
・異なる材料の投入ミスが懸念
→材料投入時QRコードで材料を照合。
一致しないと投入の蓋が開かない仕組み
など「仕組み」で不具合を防止できるような
設備の検討・導入ができると◎です。
万が一不良が発生しても流出しないように
後工程に画像検査工程を設置するなどの対策も必要です。
私の経験上、ここまで対策しても不良は出ます(笑)
世の中想定外のことばかりです。
不良が発生してしまうと
- 顧客からの信頼低下
- 会社の損失
- 選別や原因究明客先報告などの工数発生
選別とは不良が発生した際
他の出荷品に同じ不良がないか
製品をひとつひとつ再確認する作業です。
すでに出荷されていた場合は
製品の出荷先が県外であろうと確認対応が必要になります。
不良品の発生はマイナスでしかないので
「不良品は絶対に流出させない」という
強い気持ちで業務に取り組みましょう。
また
既設ラインの改造で最も注意すべき点は
新製品流動のために行う改造が原因で
既存の量産製品の流動が不可になることです。
何かあった時に改造前の状態にできるような準備
(状態の確認・記録や部品の用意)を
しておくことがおすすめです。
量産設備の改造は
慎重になりすぎるくらいがちょうどいいくらいです。
- FMEAを実施しよう
ライン立上げや設備の改造には当然リスクがあります。
そんなリスクを洗い出し
不具合の発生を未然に防止するために
「FMEA」を実施します。
この「FMEA」
管理をしっかりして記録を残していくことで
次の新製品の検討時にも役立ちます。
実際に私が前職で担当していた案件では
「FMEA」が過去の記録を含めた管理になっていたので
リスクの管理が
高いレベルで実施できていたと考えています。
「ライン立上げ/改造」でつらいこと
- 設備仕様書の作成が大変
- ライン立上げは設備導入があるので納期管理が難しい
- 設備導入/量産ラインの改造は
稼働停止日に実施することが多く休日出勤になる
条件出し
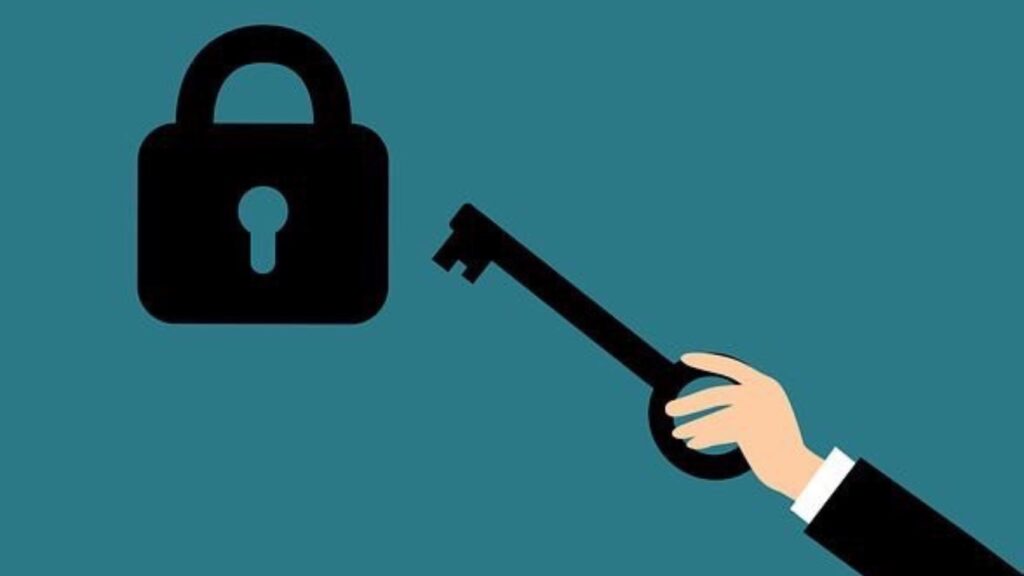
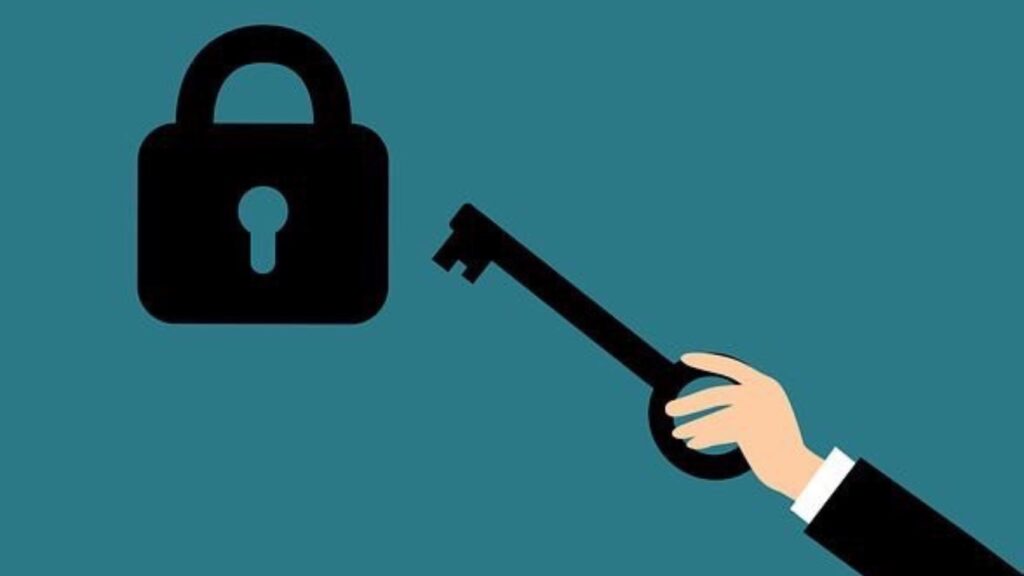
製品は条件が決まらないと生産できません。
客先からの規格を満足できるように条件出しを行います。
温度調整など内容は製品によって様々です。
初期値は過去の実績や量産の類似製品の条件などを参考にして設定します。
この条件出しでは
規格に公差内に入ればよいという考えで行うと✕
測定値のばらつきが少ない&平均値が規格中央になるように合わせこむ必要があります。
都度サンプルを提出し
客先にOKがもらえるまで条件出しを繰り返し行います。
「条件出し」でつらいこと
- 製品によっては完成までに数時間かかるものもある
- 顧客からの急なトライ依頼が来ることがある
- 既設ラインを借りる時は
稼働停止日に実施することが多く休日出勤になる - 納期が決まっているので
条件がなかなか決まらない時のプレッシャーがきつい - 条件出しを行う際
設備によっては怪我のリスクがある(高温など)
品質確認
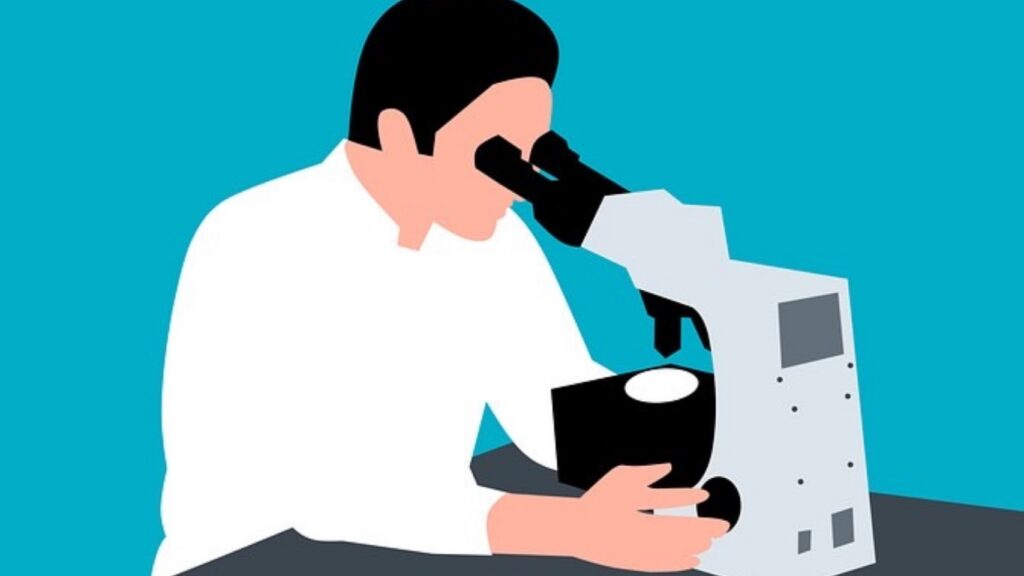
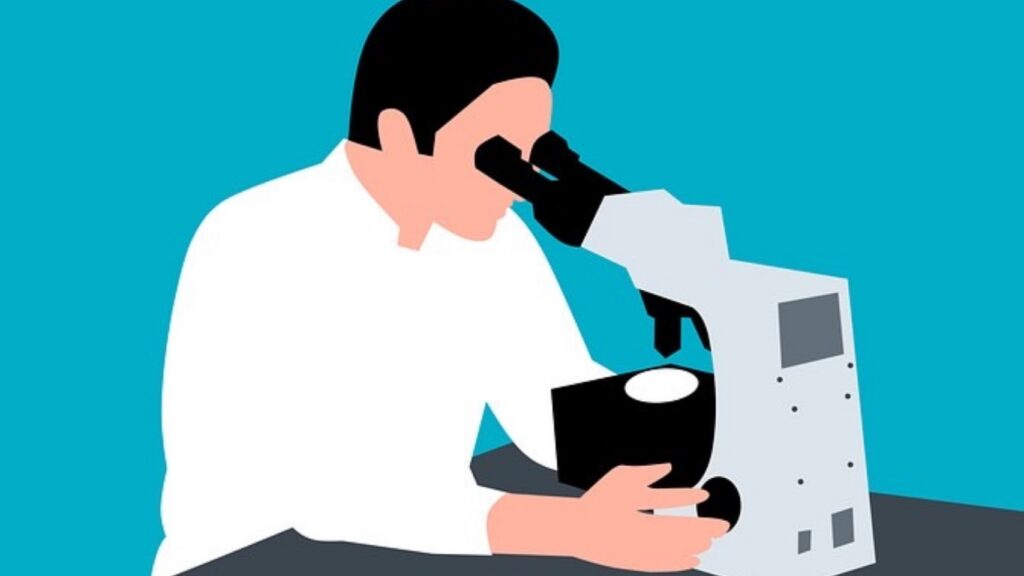
条件出しトライサンプルは客先提出だけでなく
社内測定でも客先要求を満たしているか確認します。
最低でも30個は測定を実施して
工程能力が出ていることを確認しましょう。
なので
必要なサンプル数は
顧客からのサンプル提出数+社内測定確認用になるかと。
生産技術が測定まで実施することもあれば
検査グループに測定を協力してもらう場合もあります
流れとしては
社内測定してOKだったものを
客先にサンプルとして提出→客先評価
になります。
測定者(人)によるばらつきや
使用している検査機の違いなどで
測定値が
弊社↔客先で異なりOKがもらえないこともあります。
「品質確認」でつらいこと
- 測定値が規格内でも値のばらつきがあると
OKがもらえないことがある(再測定or条件見直し) - 特殊な測定方法があると時間がかかってしまう
- 立上げ時は測定数/項目が多く
条件を見直す度の測定に多大な工数がかかってしまう
標準類作成
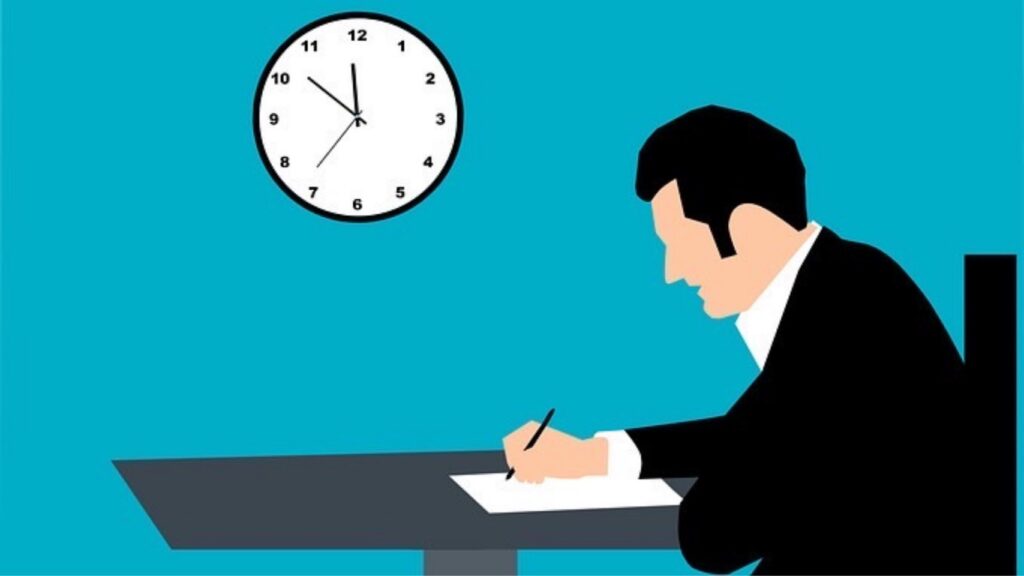
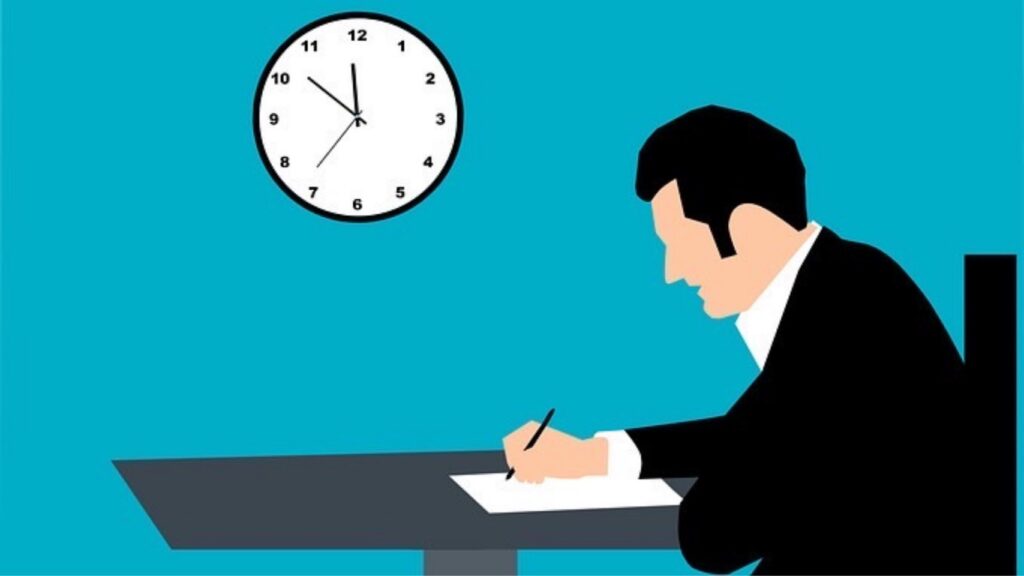
生産準備業務のひとつに標準類(作業手順書)の
作成・発行があります。
(標準類とは生産時のルールを書面化したもの)
担当者は作成後に自部署の上司に承認をもらい
速やかに関連部署へ展開します。
この展開された標準類を元に製造部は生産をしていきます。
生産技術部が発行する代表的な標準類としてあるのが
- 条件表
- 作業指示書
- QC工程表(品質保証部が作成担当の会社もあるかも)
“条件表”はその名の通り
製品(良品)を作る為の条件が指示されており
製造はこれを見て設備の温度条件などを設定します。
“作業指示書”もその名の通り作業方法が指示されています。
材料を入れる順番や設備起動の方法など
生産時の作業者の動きが細かく記されています。
“QC工程表”は材料の受け入れから出荷までの流れや
各工程での品質管理方法を記載した書類です。
各製品、品番ごとに細かく存在します。
他にも
製品の検査するポイントを記した検査指示書
設備の点検について詳細を指示する点検指示書
などがあります。
この標準類もすべて量産前(初品段階)に
準備しなければなりません。
会社によって呼び方や必要書類、発行部署は異なりますが
量産前に多くの書類の準備が必要なのは同じです。
また
作業指示書やQC工程など
量産前に客先から提出を求められる書類もあります。
客先としても
- 品質の管理方法が明確になっているか
- 作業指示が明確になっているか
- 必要事項がルールができているか
などを確認する必要があるからです。
これらの標準類は
修正があった時の為に
提出期限が量産日よりも1ヶ月程度早く設定されるなど
納期設定が厳しい場合もあります。
「標準類作成」でつらいこと
- 作成が必要な標準類が多い
- トライで生産条件が決まるまで作成が開始できない
- 標準類ができないと生産ができない
- 当初の計画よりも短い期間での作成が必要になりやすい
- 設備導入や条件出しなど
重要な現場作業と並行して書類作成の時間確保が必要
初品
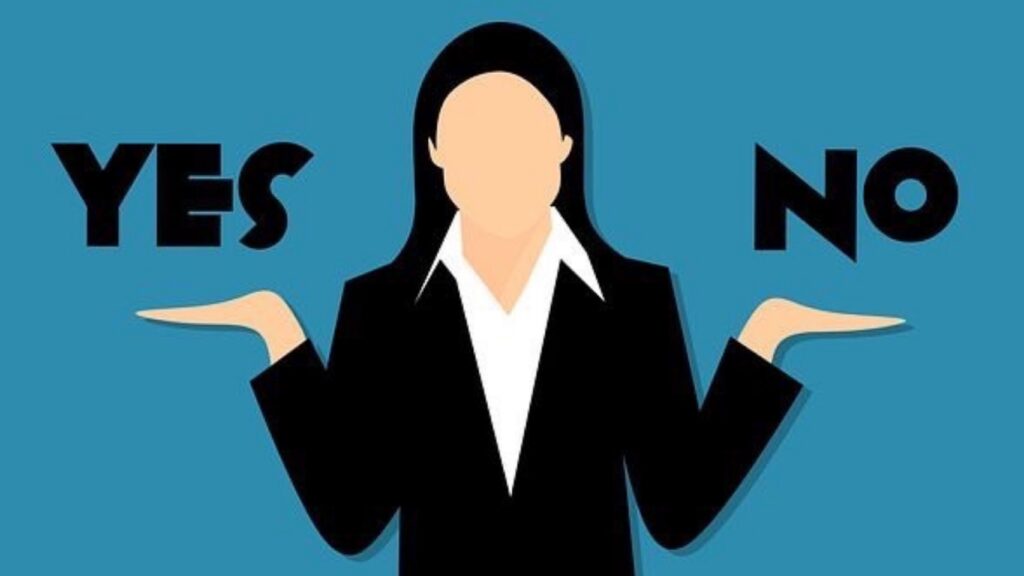
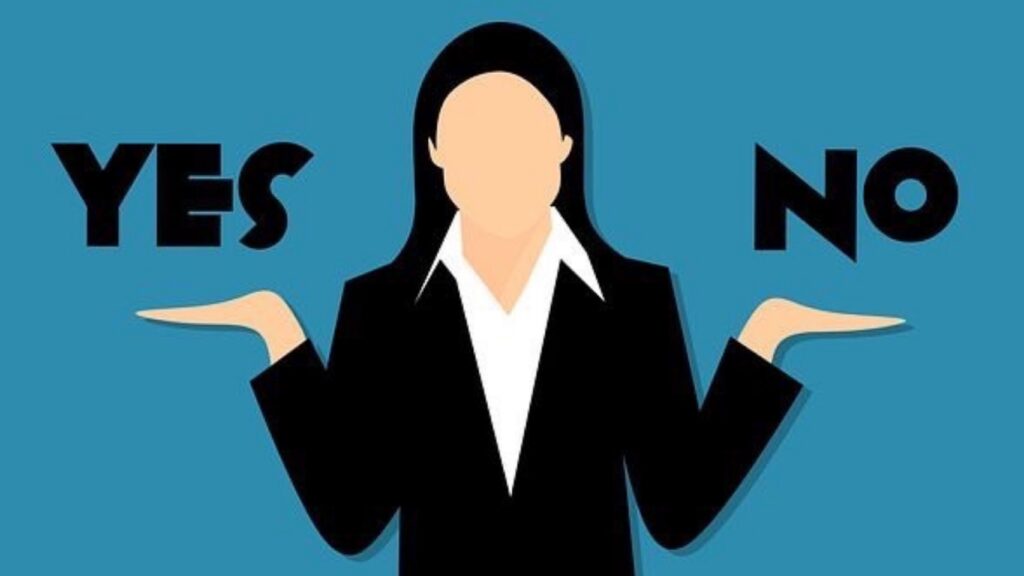
量産前に最終確認を行います。
この段階はすでに
「量産と同じ」という感覚で問題ありません。
「この製品をこれから量産していきますよ」
ということを客先へ確認するイベントになるので
量産と同じ準備・生産・検査・出荷で
量産同等品としてお客さんにサンプルの提出を行い
量産移行へのYES/NOの判定を行います。
「初品」でつらいこと
- 初品は量産同等品なので
大きなミスが許されないプレッシャーがある - 初品段階で各部署を量産同等の作業可能な
状態にしておかなければならない(特に製造部) - 初品での不具合・客先指摘事項は
すぐ目先の量産までに修正完了が必須なので短納期
量産
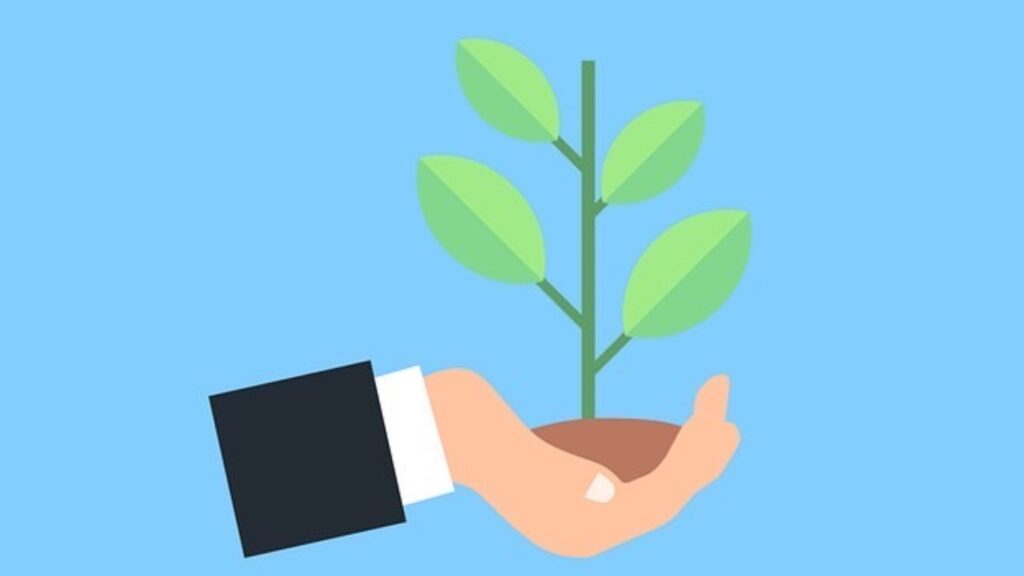
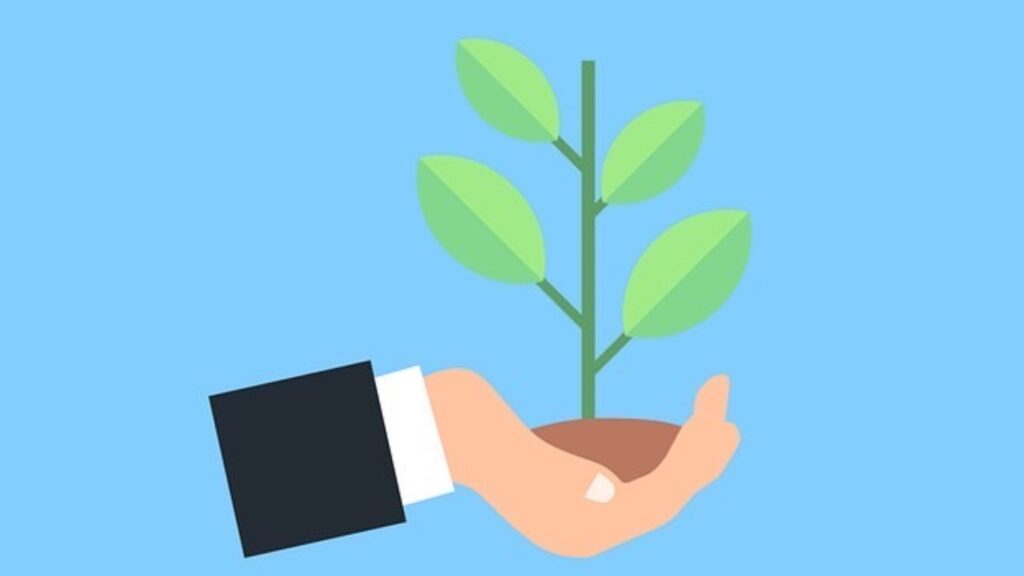
初品生産で見つかった懸念点・準備不足だった点を
改善して量産へ移行します。
初品生産=量産という考え方なので
基本的に大きな改善点はないはずです…
生産準備としては
初品を乗り越えると
気持ち的に少し落ち着くことができます。
「量産」でつらいこと
- 量産での不具合は客先に大きな損害を与えてしまう
可能性がある(これは常に感じていること)
初期管理
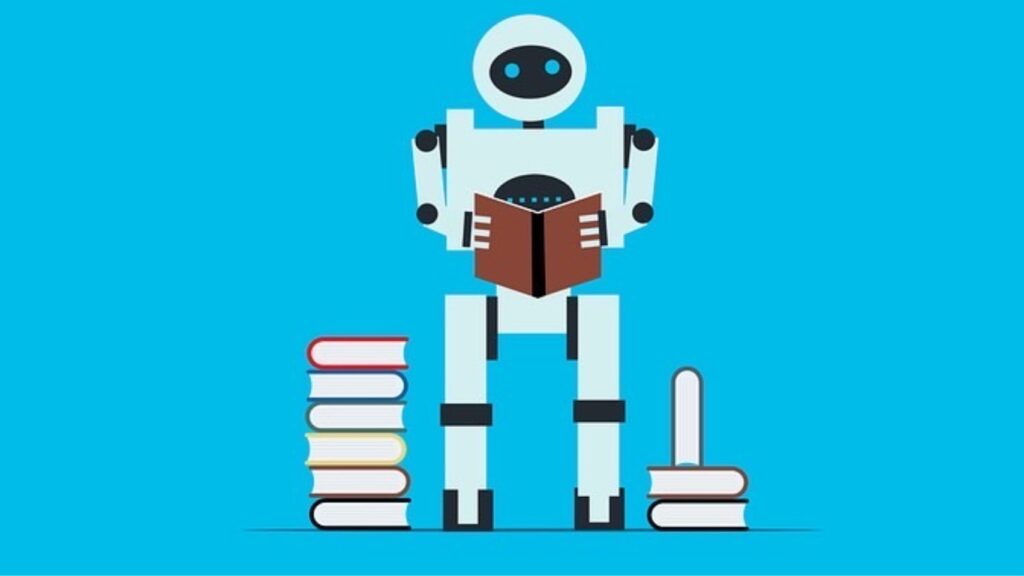
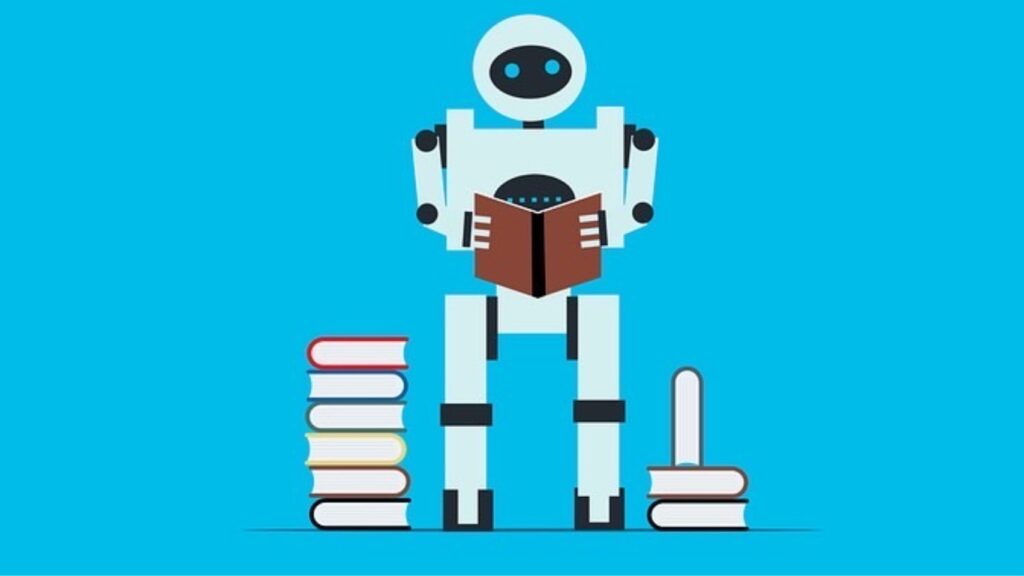
量産へ移行したから完了という訳ではありません。
量産開始後の数ヶ月は
特に入念な品質確認が必要になります。
量産開始後すぐの製品を「初期管理期間」に設定し
普段の定期測定よりも
頻度や確認数・測定項目を増やします。
この期間に関しては会社ごとに異なりますが
私が勤務していた会社では3ヶ月と設定していました。
3ヶ月初期管理期間として対応し
問題がなければ各部署で最終確認後
通常の量産工程へ変更します。
「初期管理」でつらいこと
- 初期管理期間は客先も要確認するので細かい指摘がある
- 量産後すぐはトラブルの発生率が高いので
都度対応に追われる
工程改善
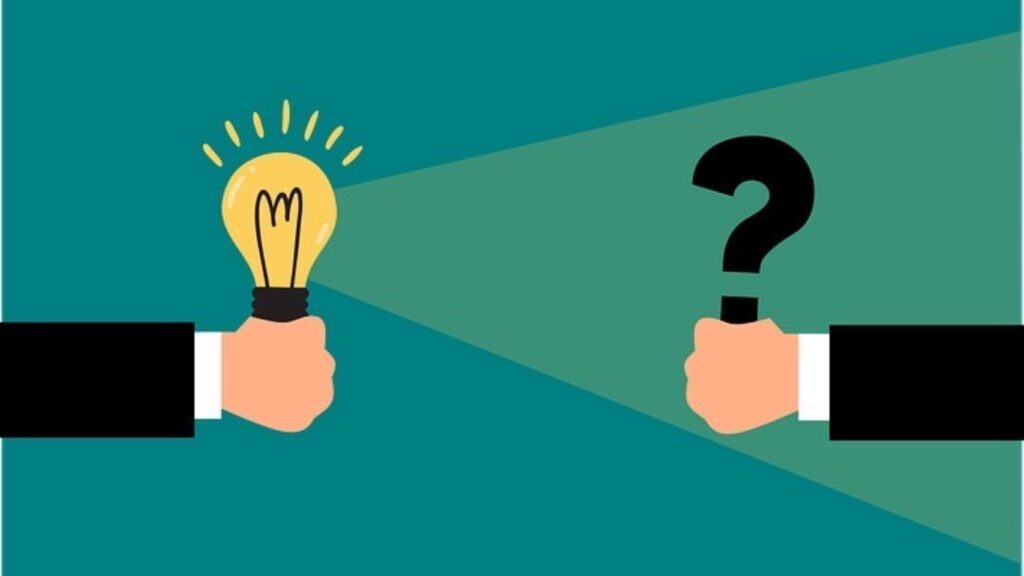
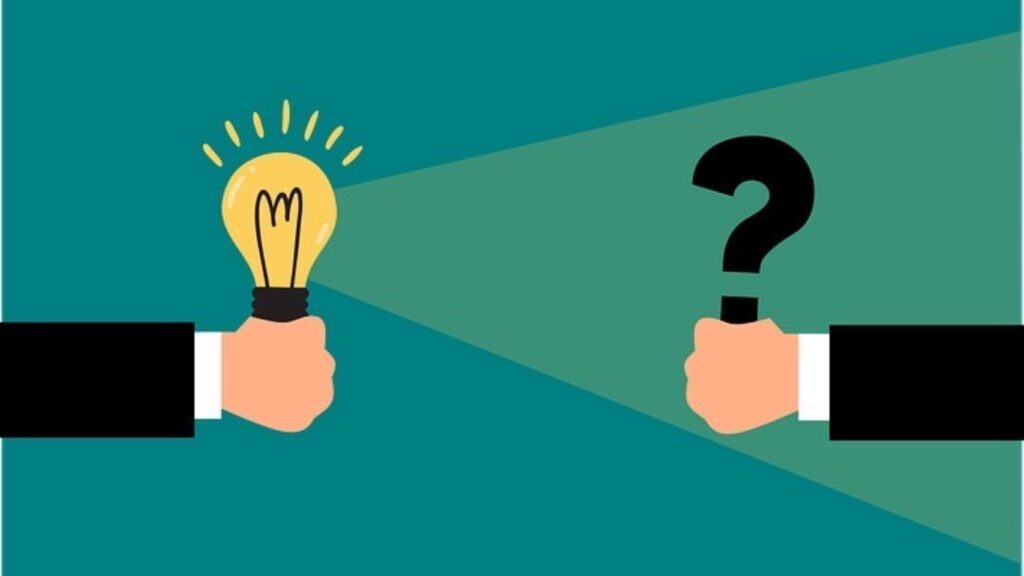
新製品の立上げをしながら…
工程改善も業務のひとつになります。
設備改造により人件費の削減や不良低減など
会社の利益率を上げる業務です。
合理化(不要な点を除き能率的にする)や原価率低減の活動
自働化による人件費削減や不良率低減などの活動をします。
近年ではAGVや協働ロボットが注目されていますね。
会社によっては
生産準備と工程改善でチームが分かれていることがありますが
私が所属していた会社では
生産技術部/生産準備チームが「工程改善」も担当していました。
「工程改善」でつらいこと
- 利益率が計算通りにいかないことがある
(設備停止のばらつきなど) - 不良発生の原因究明が大変
(原因究明のための不良再現トライ) - 製品の生産準備業務との両立が大変
トラブル対応
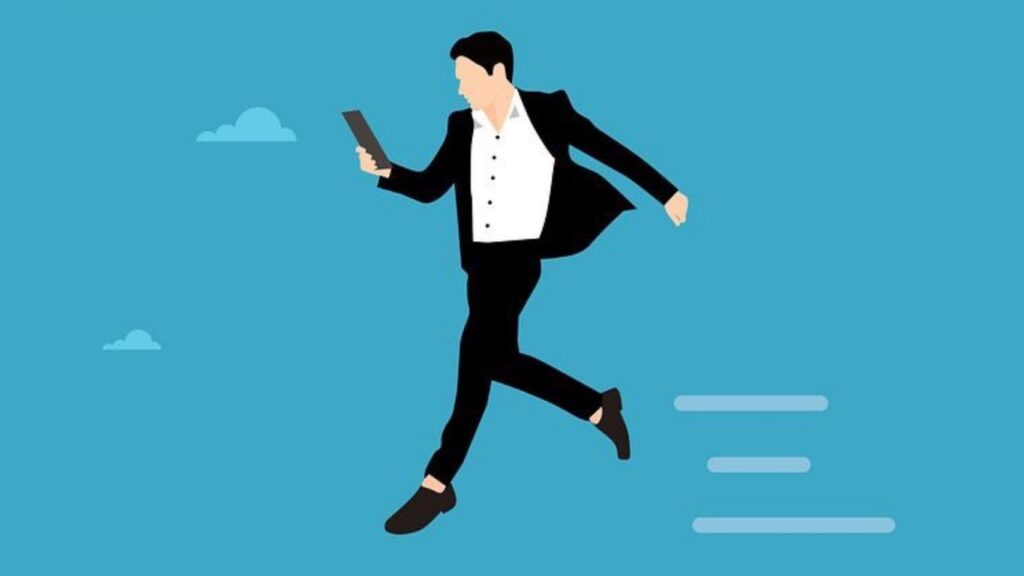
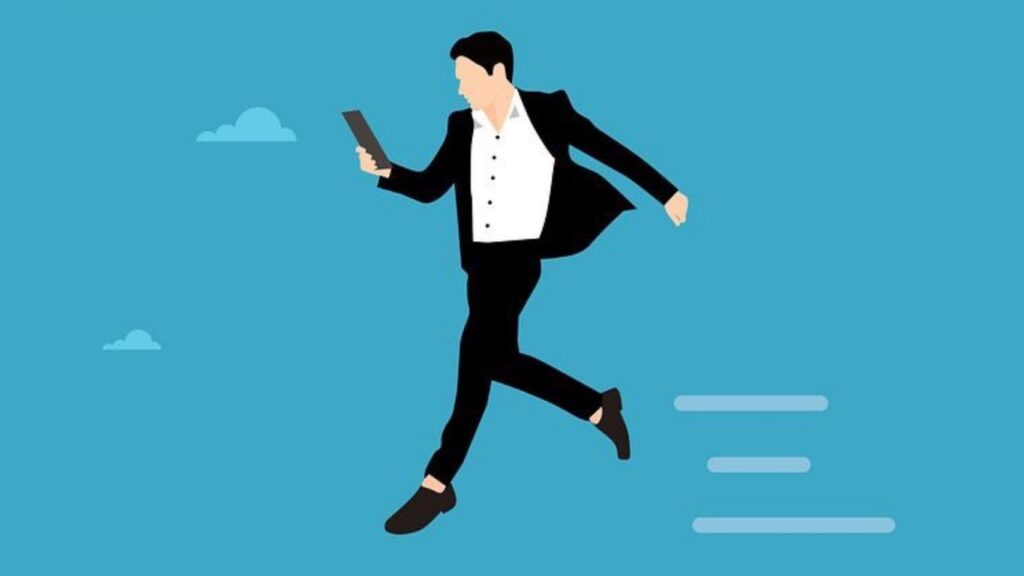
生産準備で立上げたライン・設備についてのトラブルは
担当者である生産準備チームが詳しいので
製造からすぐに声がかかります。
突発的に発生する問題に対して
最善な解決策を考えるのも重要な業務です。
特に
生産が止まってしまうような異常が発生した場合は
最優先での対応が必要になります。
まずは暫定でもラインを復帰させることを1番に考え
復帰後は恒久対策の方法まで検討します。
復旧対応時に
設備の重要部品(製品と接触のあるユニット)
を交換した場合は
品質に問題がないかも必ず確認しましょう。
量産工程では部品交換など些細なことでも生産状況が変化した場合(変化点がある場合)は必ず製品の品質に異常がないかを確認すること。
ただでさえ
定時で収まりきらないようなボリュームの
多忙な通常業務に加えて突発案件…
生産技術部の残業が多くなる大きな要因ですね。
「トラブル対応」でつらいこと
- ライン停止など対応が早急なトラブル発生時は
業務計画の見直しが必要 - 突発で想定外の業務が増える
- 設備の完全停止などの大きなトラブルで
莫大な時間が取られてしまう時がある - トラブル対応のために休日出勤が必要になる場合がある
生産技術の生産準備で働く
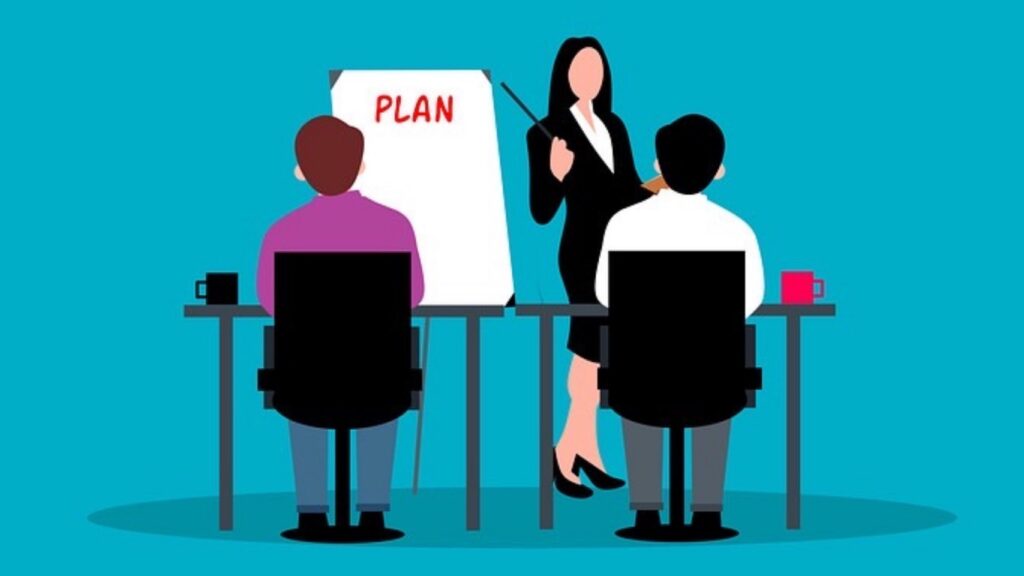
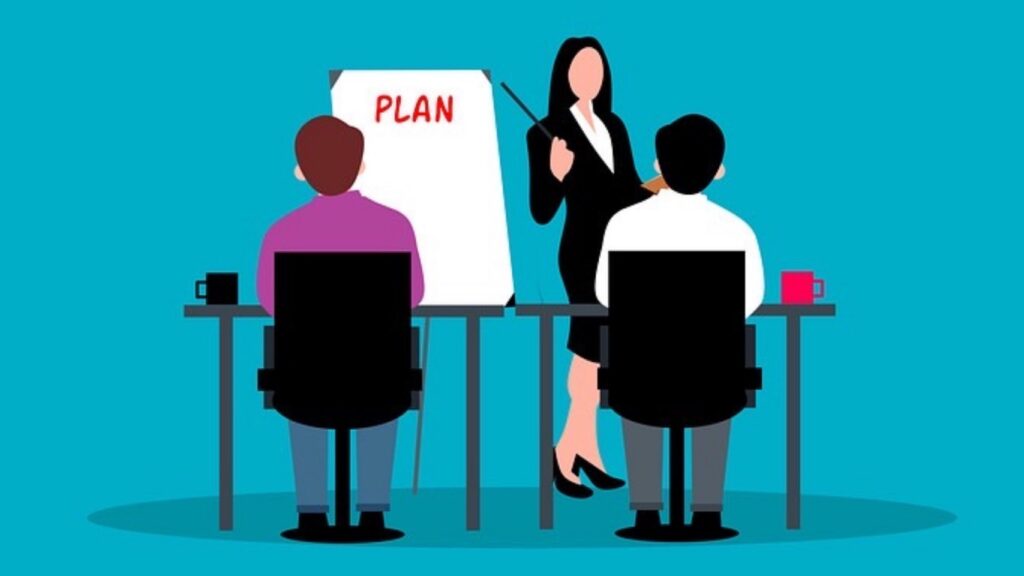
業務が自分に合っている/合っていないの判断は
実際に本人が経験しないと答えが出ません。
自分が仕事に求めるものは何かを明確にしましょう。
ここまでの解説である程度
生産技術の生産準備について理解が深まったと思います。
生産準備に配属されたばかりの人/配属予定の人。
具体的な業務イメージが湧いてきたんじゃないでしょうか。
やる気が高まったなら尚良しです。
興味を持って調べてみたという人。
期待通りの業務内容でしたら
生産準備を第1希望にするのも良し。
イメージと違ったなら他業務を調べてみるのも良し。
すでに配属が決まっているが不安な人へ。
「やりがい」は保証します(笑)
検討~量産まで工程に深く携われるのは生産技術だけです。
工程を作り込むことが「楽しい」と感じる人は少なくありません。
私も実際に「楽しい」と感じる瞬間があります。
それでもどうしても自分には合わないという人。
生産技術として
数年経験を積めば転職市場で有利に立ち回りやすいので
ポジティブに前を向いてがんばってください。
生産技術を経験しておけばどんな職種もへっちゃらです(笑)
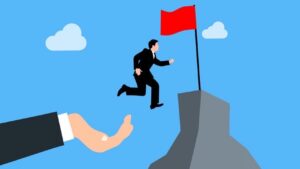
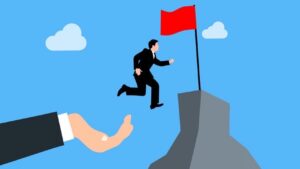
生産技術の生産準備として2社でキャリアを積んで思うこと(余談)
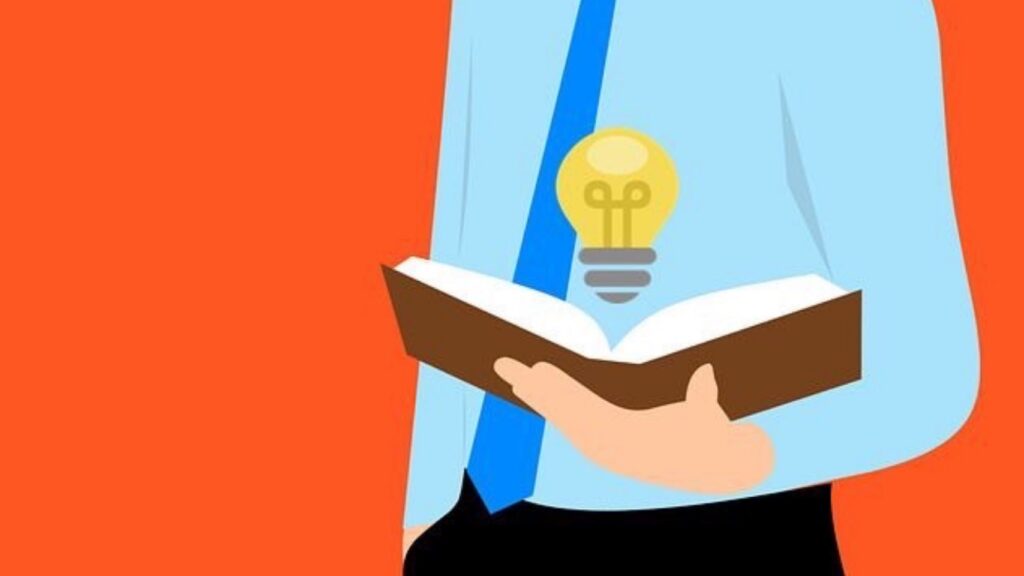
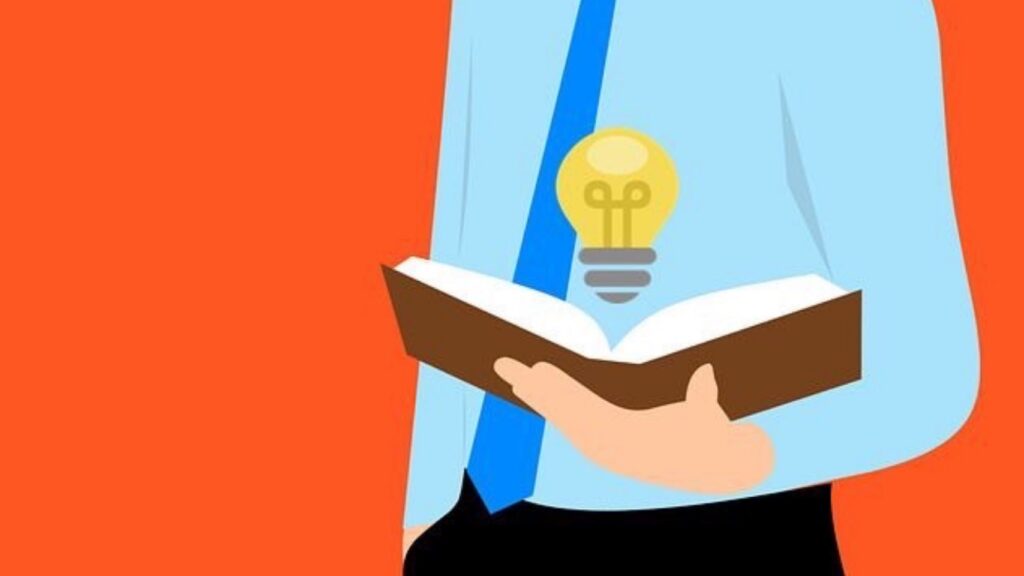
私自身ここまでのキャリアで数年間
実際に生産準備の業務を行ってきましたが
業務内容の幅が広いため多忙でほぼ毎日残業。
休日出勤も多く大型連休を丸々休めた記憶もあまりないため
正直ワークライフバランスが充実しているとは言えません。
設備に関わることもあるので
大きな怪我をするリスクもありました。
それでも
ラインが立ち上がった時には
大きなやりがい/達成感を感じますし
製造の人たちが
自分を頼ってくれる時には嬉しさもあります。
忙しいからこそ大きなやりがい/達成感を感じることができる
そんな業務なのかなと思います。
ガツガツ仕事をしたい人に
生産準備業務は大変向いています。
残業代+休日出勤手当もありますので(笑)
体育会系の人が多いイメージで
人事も意識して配属している印象を受けました。
デスクワークと現場仕事の絶妙なバランスで
気分転換しながら仕事ができるのが
生産技術/生産準備の良いところだと思います。
しかし
まったり仕事をしたい。
パソコンを使って基本的には座ってできる業務をしたい。
と言う人には不向きな職種ですので
生産技術の生産準備は人によって
合う/合わないが大きく分かれる職種だと思います。
まとめ
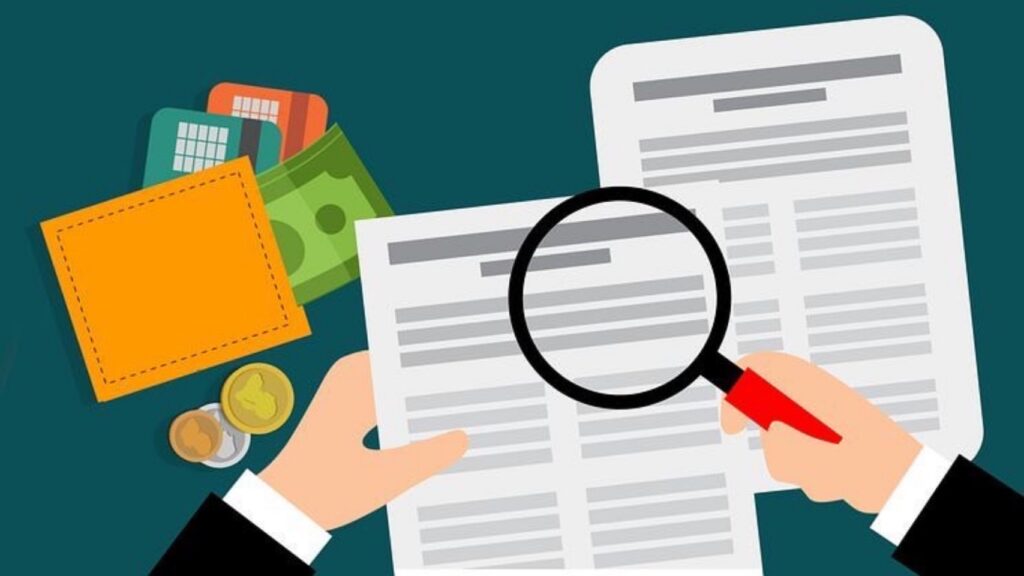
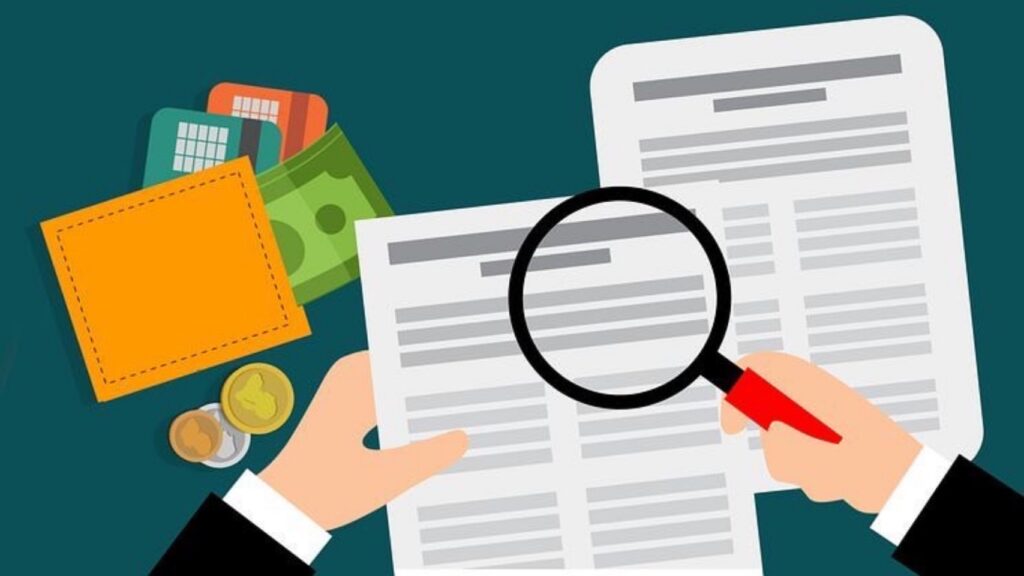
いかがでしたでしょうか。
長くなりましたが
今回は
「生産技術の生産準備はつらい?具体的な仕事内容は?」
について解説しました。
まとめです。
・見積図の入手から量産までの各ステップごとに
必要事項を把握して業務に取り組む
・生産準備の業務内容は
工程改善/トラブル対応など多岐に渡る
・忙しくて大変だからこそ大きなやりがい/達成感を
感じることができる
・人によって合う/合わないの感じ方の差が大きい
生産準備は
部品をラインで大量生産しているメーカーには
必ず存在する職種なので
大人数が生産準備業務に携わっています。
その中のひとりに
「なった」もしくは「なりたい」と感じているあなたが
ここまで
本記事を読み進めた姿勢は素晴らしいです。
その高い意識をこれからの業務にもぜひ生かしてください。
みなさんが
理想のキャリアプランを描けることを願っています。
それでは、このへんで。
コメント