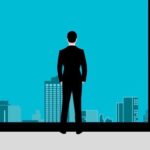
メーカーの生産技術職に興味があるけど
自分って向いているのかな…?
大変って話もよく聞くけど
具体的にどんな仕事内容なの…?
気になるけど一体誰に聞けばいいんだ…
そんな悩みに
自動車部品メーカー2社で生産技術部としてキャリアを積み
且つ、現役の生産技術部員である私が答えます。
- メーカー生産技術の具体的な仕事内容
- メーカー生産技術に必要な知識・資格
- メーカー生産技術の大変なこと
- メーカー生産技術に向いている人
就職・転職活動中や入社後の配属の前に
メーカーの生産技術って
具体的にどんな仕事内容なのか。気になる時ありますよね。
私も新卒で就職活動している時は
気になって調べていました。
そんな悩みを持つ人たちへ向けて
今回は
メーカー生産技術部の仕事内容について
詳しく解説していきます。
本記事は
現役生産技術部員の「生の声」になります。
実際の経験をもとに
例を出しながら非常に分かりやすく解説していくので
読み終えた頃には
メーカー生産技術の仕事内容について
理解が深まっているとともに
自分がメーカーの生産技術に向いているのかどうかも
分かると思います。
※経験を踏まえた個人的見解が含まれる事をご了承下さい
それでは、さっそくみていきましょう。
メーカー生産技術の仕事内容と向いている人について現役の生産技術員が解説
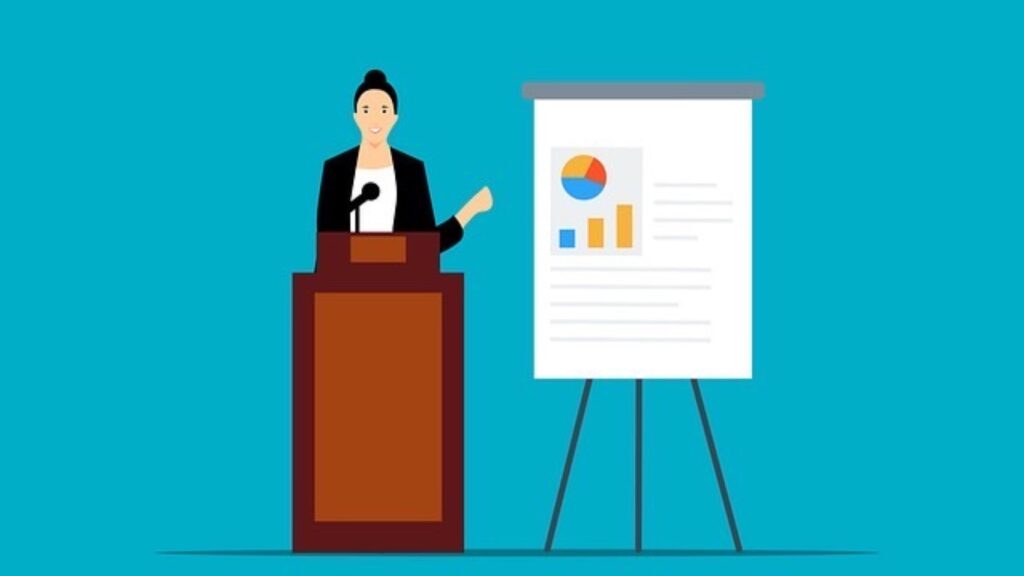
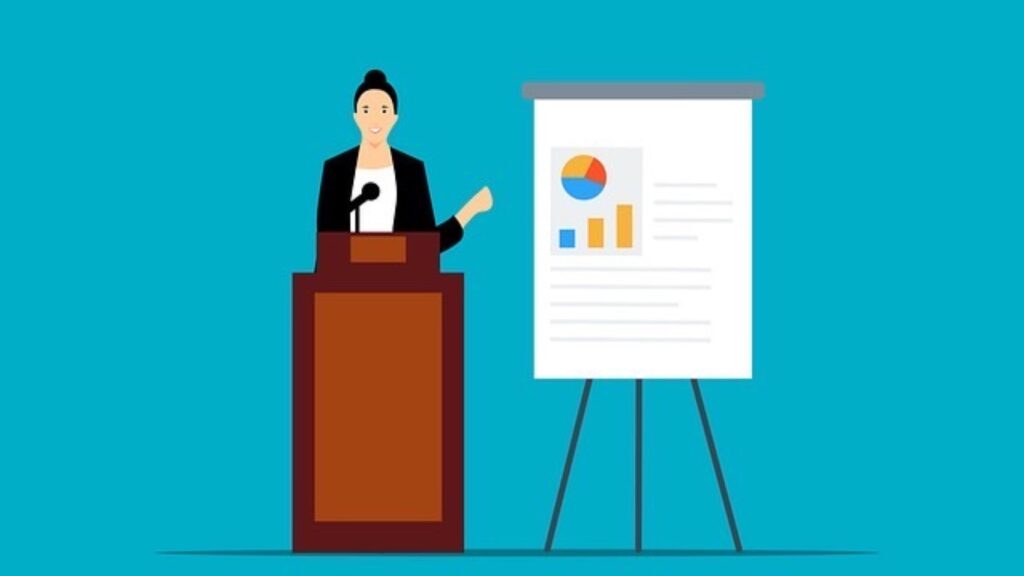
メーカーの生産技術の仕事内容は大きく
工法開発・生産準備・工程改善の3つに分けられます。
仕事内容はチームで分けていたり
1つのチームで上記のすべてを担当したりと
会社の方針によって異なります。
私の経験上だと
「工法開発のチーム」と「生産準備&工程改善チーム」
という2チームに分けられていました。
それぞれの具体的な仕事内容をみていきましょう。
メーカー生産技術の工法開発
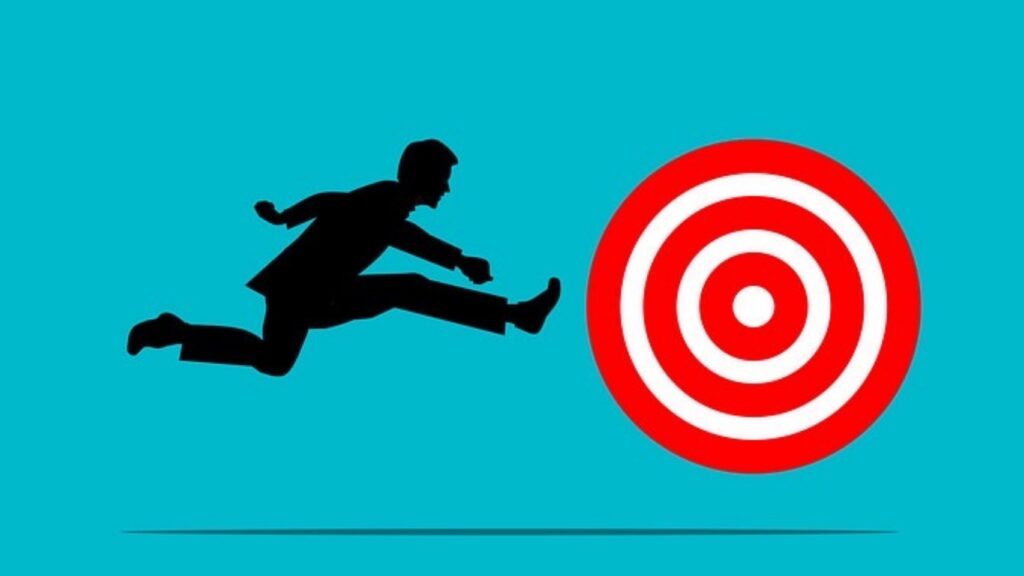
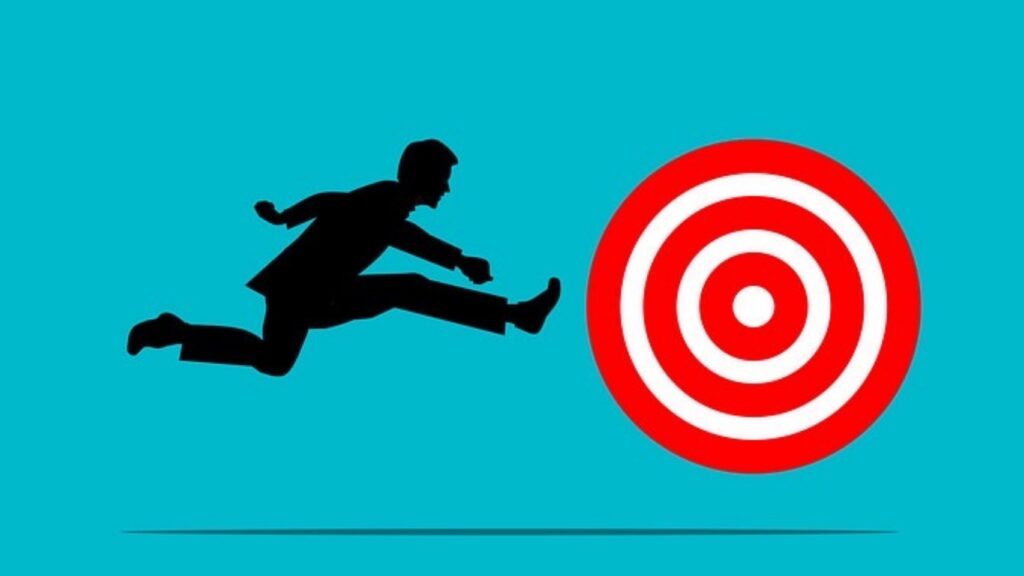
メーカー生産技術の仕事内容のひとつめ
「工法開発」は
製品を生産している量産工程の新たな工法の開発業務です。
いきなり「開発」と言われても
イメージが湧かないと思うので
具体例を挙げて説明します。
例① サイクルタイム低減
ある製品の加熱処理時間の時短を検討します。
今まで100秒で処理していた工程の処理時間を1秒でも低減させれれば、生産性が上がりますよね?
この時短条件を実現させるための業務に取り組むのが「工法開発」です。
事前検証でざっくり処理時間を100秒→80秒程度まで低減できる目星をつけた後
当然トライが必須ですので
サンプルの作成からスタートします。
まずトライ条件ですが私なら条件を
100秒 90秒 80秒 70秒 60秒くらいで振り分けて
各n=30ほどでデータ取得をすると思います。
※n=30の理由は工程能力を出す為
80秒だけとれば良くね?と思った方は
まだまだ初心者です(笑)
100秒サンプルの理由:そもそも時短条件が実現可能となる為に必要なことを考えると分かります。
新しい工法の承認をもらうには、その工法でできる製品の能力が既存品と同等/もしくは規格を満足していなければいけません。
その為、量産品との比較用としてこの100秒サンプルは必要になります。
90秒サンプルの理由:目標の80秒がNGとなった場合、10秒でも時短できる可能性を模索するという意味合いです。
70秒と60秒サンプルは予想よりも効果がでる可能性があるので、その確認用です。
検討→計画→サンプル作成→評価→結果まとめ→上位報告→顧客報告→承認といった流れで
新しい工法をどんどん織り込んでいき会社の利益率アップに貢献します。
例② ロボット導入
手作業で行っている工程へロボット導入の検討です。
人件費とロボット導入費を比較して何年で設備代(ロボット代)を回収できるかなど細かい利益率の計算が必要になります。
・現状の人件費は?
・ロボットの導入費は?
→ロボットの購入費は〇〇年で回収できます
→以降利益
→ロボット購入費回収後は1日当たりの
〇〇円の利益が生まれていくのか?
「工法開発」は、やみくもに新しい工法を開発するのではなく、その実現性や検討した工法が実現した場合に具体的にどれくらいの利益がでるのかを計算して明確にすることが必要です。
会社にもよりますが遅くても2年後あたりから利益が出始めないと承認は難しいと思います。
メーカー生産技術の生産準備
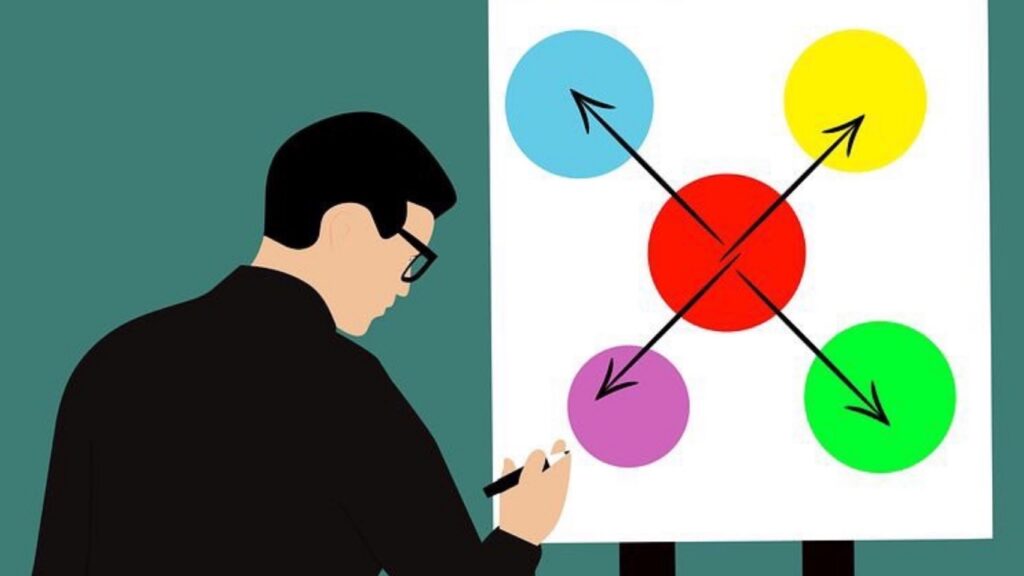
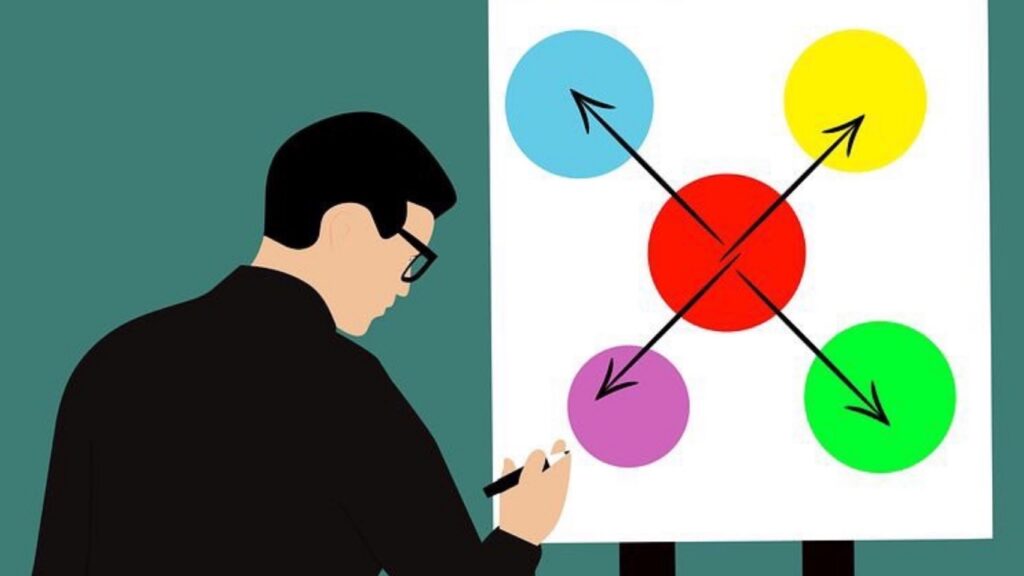
メーカー生産技術の仕事内容ふたつめ
「生産準備」はその名の通り
製品を生産できるようにする為の準備をします。
新設・増設関わらず量産予定製品すべての準備担当です。
ざっくりとした業務の流れとしては
検討→DR→検討→DR→量産→初期管理
DR(デザインレビュー)は簡単に言うと関係部署で集まって問題点を洗い出す場のことを言い
会社によってDRを行う回数や細かい方法は異なります。
要は
製品や設備ごとに随時検討と確認・修正を繰り返して
量産までに
製品を生産できる状態を作り出すということです。
検討の段階で製品の販売価格についての話などもあり
工程でかかる費用に関しては生産技術部が詳しいので
普段は営業が窓口として対応してくれている顧客や
調達が対応してくれている構成品(材料)の仕入れ先など
との打ち合わせにも参加することがあります。
製品検討会
お客さんから要望の製品について各部署と検討会を実施します。
生産技術での議題としては
- 既存設備での流動可否
- 既存生産能力で対応可否
- 客先要求品質確保の可否
他、問題点
要は
- 全く新しいラインの新設なのか
- 増設なのか
- 既存ラインの改造が必要なのか
- 品質は確保できるのか
- 条件出しのみの対応で可能なのか。
などを検討します。
設備検討・導入
生産準備がが最も他社と関わりを持つことになるのが
この設備関係です。
設備導入が必要となった場合は
商社、メーカーと仕様の検討をします。
すでに実績のある同様のライン増設でも
何かしらレベルアップさせる為に
既存ラインでの問題点などを洗い出します。
生産技術として同ラインの増設となると
細かいことでもいいので、何かしらのレベルアップは当たり前だと思ってください。
例えば
機構を変えることで既設と生産能力は同等だが価格は安いなど。
些細なことでもレベルアップを検討します。
同時にレイアウト検討や墨出し
(設備を置く位置をマーキング)も行います。
また
設備導入の際
特に注意しなければならないのが「安全」です。
- 非常停止はキノコ型ボタン
- エリアセンサーのピッチは指検知
- 自動起動は両手でスイッチを押さないと起動しない
など、労災を起こさない仕組みづくりが重要です。
各会社の安全基準によりますが
大企業であればあるほど安全条件が厳しくなる傾向があります。
例に挙げた内容の意図は下記です。
キノコ型ボタン
→非常停止はいざというときに押しやすいキノコ型
エリアセンサーのピッチ
→指を怪我しないように指も検知可能な仕様にする。
両手起動(両手でスイッチを押さないと起動しない)
→両手起動で設備の挟まれを予防(基本的にどの会社も全設備両手起動)
この辺に関しては設備導入のたびに確認することなので
経験を積むと、確認すべきところが分かってきます。
重要な内容は打ち合わせ時に
しっかりとメーカーに話をして間違った認識がないか
十分確認をしておくことが大切です。
その場はもちろんですが
発行される議事録にも必ず目を通し
認識違いがあればすぐに確認・訂正が必要です。
間違った内容が記載された議事録が残ってしまうと
価格など揉め事の要因になるので
議事録は発行当日に確認するのが〇です。
安全は何よりも優先
「安全」が二の次だという会社は聞いたことありません(笑)
メーカー生産技術部としてこの精神は忘れてはいけません。
次に「品質」です。
「生産技術」としては工程内の不良発生を防ぐ仕組みを検討します。
例えば、材料誤投入などの作業ミスが起こらないように
材料が違うと設備の仕組的に起動できなくさせるなど
「ポカヨケ」の機能の追加を検討するなど
(材料↔設備間で正誤を照合確認するQRコード承認方式)
「作業ミスは人ではなくて仕組みを責めろ」と言うように
作業ミスが物理的に起こらないような仕組みを設備に備える。
そんな仕組みを考えることも生産技術の仕事のひとつです。
「安全」「品質」ともに
レベルアップや改善をしようとすると
設備知識が必要となります。
細かい部分は要望をすればメーカーが対応してくれますが
自分が担当しているラインの設備に関しては
ある程度の知識は持っておくべきです。
←生産技術として経験を積んでいれば、知らぬ間に経験値として蓄積されていきますが…
条件出し(サンプル作成)
生産の「核」となる部分です。
コツは実績のある類似品を参考にすること。
製品によって項目は多種多様ですが
お客さんの要望に沿った製品となるように条件を選定します。
ここでのポイントは規格の「狙い値」です。
製品には規格があり公差があります。(上限・下限)
量産前の条件出しでは製品の各測定値が規格の中央値になるように意識して調整します。
規格ドンピシャは難しいと思うので
上下限を狭めて確認するのが良いでしょう
(規格が±5なら条件出しは±3でやるなど)
サンプル検査・評価
設備導入・条件出しが完了したら
その「確からしさ」を証明するために
サンプルの作成→検査・評価をして工程能力を出すことで
問題なきエビデンス(証拠)にします。
評価は客先から提出される
「検査指示書・製品規格書」(呼び方はいろいろあります)
に沿って行います。
初期管理
「生産準備」ですが
量産後すぐの製品に対しては確認が必要です。
量産が始まってすぐは初期管理期間として
通常よりも製品の定期測定の数や測定項目を増やして対応します。
この期間は会社にもよりますがだいたい3ヶ月ほどで
問題なきことが確認出来たら通常量産品対応へ移行します。
この期間は製品だけでなく
設備にも異常がないかマメにチェックしましょう。
海外ライン
海外の子会社などでライン立上げを行う際は
はじめに国内で設備の調整・試運転をしてから
海外へ持っていくことが多いです。
国内のライン新設と同様のステップ+現地確認になります。
基本的には現地へ行きSV(監督者)として
最後まで面倒を見ますが
リモートで実施することもあります。
「生産技術/生産準備」の海外業務は赴任だと
海外拠点の社員にノウハウの伝授などがメインになりますが
出張ベースとなると大半がライン立上げなどの
設備関連業務になると思われます。
生産技術/生産準備の業務に関しては
下記でさらに詳しく解説しています。
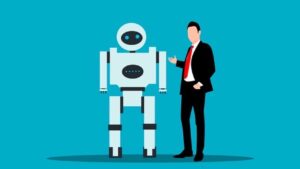
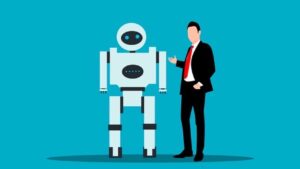
メーカー生産技術の工程改善
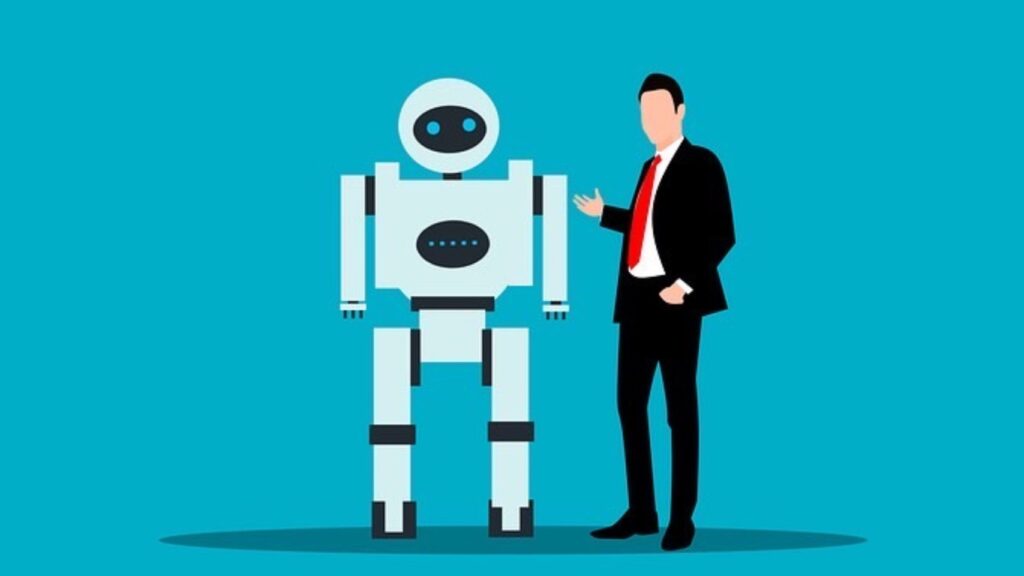
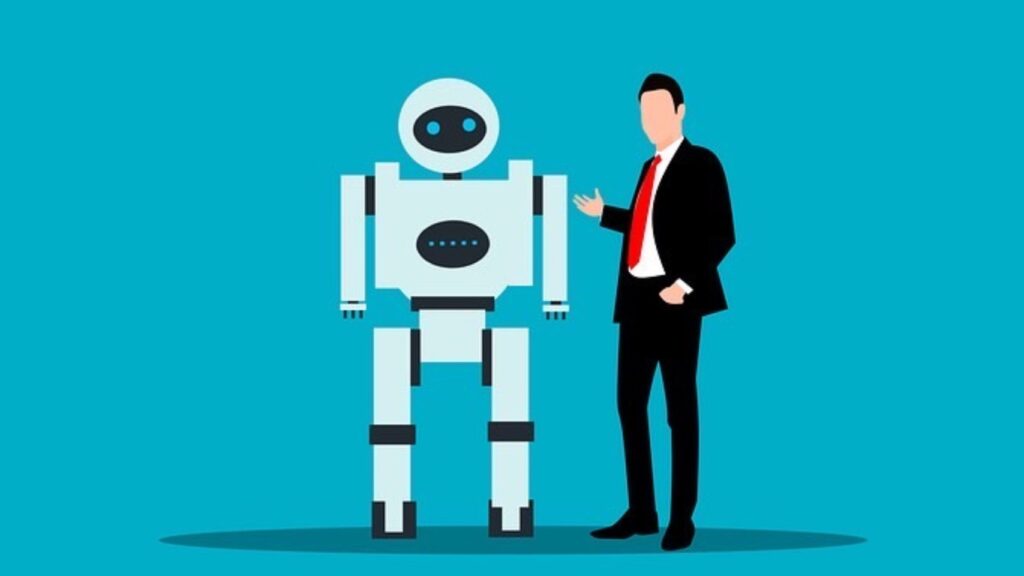
メーカー生産技術の仕事内容みっつめ
「工程改善」は
既存の工程を改善し会社の利益アップに貢献します。
不良改善
工程内で不良が発生した場合は
原因を究明し、解決しなければなりません。
具体的にどのように原因究明をしていくかというと
不良の内容から発生する可能性のある工程を洗い出し
再現トライを実施することで発生源を見つけ出します。
その後
改善策を検討し、ここでもトライを実施します。
案がいくつも出た時はすべてトライで確認し
最も良い内容を改善案として採用します。
トライの実施に伴い
特注のトライ用治具が必要となることがあるので
作図・図面読解能力やCADのスキルがあると便利です。
図面に関しては製品図面の読解力も必要なので
簡単な幾何公差の知識は勉強しておくべきです。
主に業務は
不良発生→原因究明→改善→効果確認
のステップで進めていきます
原価低減
会社の利益を上げる方法は売上を増加させる以外に
「原価低減」があります。
具体例を挙げます。
・2人で作業している工程を1人にする
1人が運搬、もう1人が検査という2人作業の工程を
1人で運搬・検査を行うことで
CT(サイクルタイム)が目標値に間に合うので1人作業にします!
→1人分の工数が削減できます。
・不要な工程の廃止
中間検査と最終検査で確認項目の重複があるので
最終検査のみで可能と判断して中間検査を廃止する。
→中間検査にかかる工数が削減できます。
このような
原価低減を実現する業務も会社にとって重要です。
現場の声を聞く
常に作業者(現場)から
「やりにくい」「もっとこうしてほしい」
といった声を吸いあげ
実現性があるものなら改善して生産性を向上させる。
といったことも生産技術の重要な役割の1つです。
メーカーの生産技術の資料作成
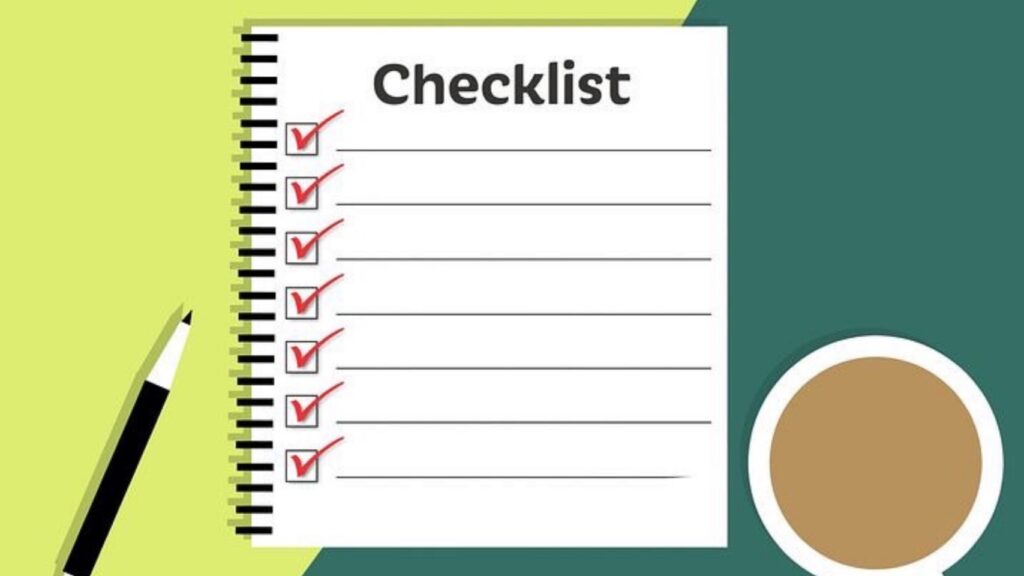
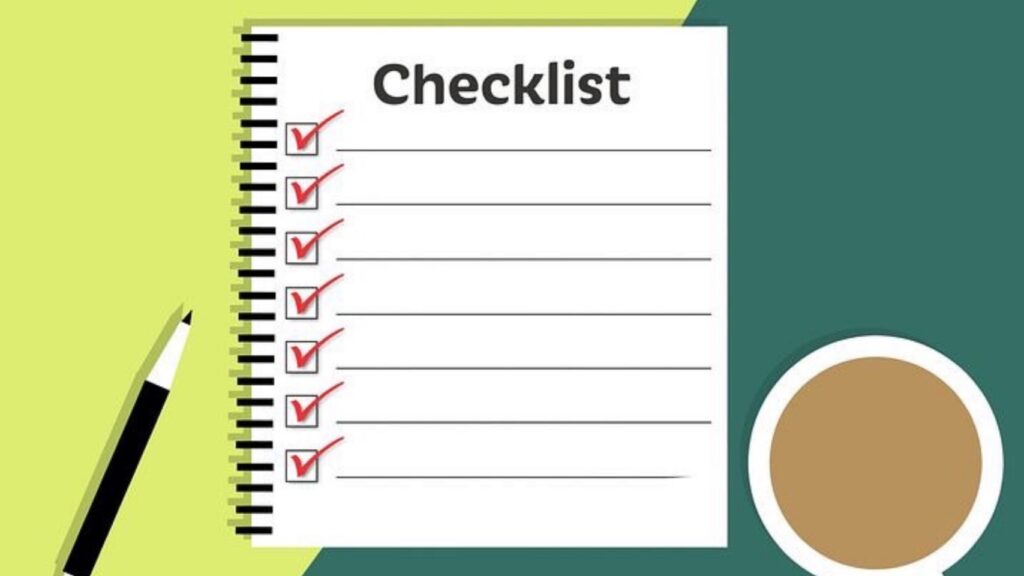
生産技術が作成しなければならない資料は多数あります。
・工程変更届
→客先に承認を貰う為に必要
・条件表
→ 製品によって変わる設備の条件(設定値)を明確にしたもの。
・作業指示書
→ 工程の作業順序を明確に記載したもの。
・点検指示書
→ 設備の点検方法を明確に記載したもの。
・検査指示書
→ 製品の検査方法を明確に記載したもの。
・QC工程表
→ 原材料の入荷から完成して出荷するまでの工程の流れを記載したもの。
→ 不具合発生時の調査や新人に工程を説明する時に使用できます。仕入れ先にQC工程表の提出を求める企業もあります。
・FMEA
→ 設計の段階で問題点を洗い出しておくことで不具合を未然に防ぐのが目的です。
・設備仕様書
→ 設備導入時にメーカーへ送付する設備の詳細などを記載したもの。
・トライ計画
→ トライの内容や日程を明確にしたものです。
・検証結果
→ トライなどの検証結果をまとめたもので、内容に応じて表やグラフにまとめることが望ましいです。
他にも会社ごとで上記資料がさらに細分化されていたり
独自の資料が存在する場合もあります。
原価関係の資料も生産技術が対応したりとさまざまです。
メーカーの生産技術のトラブル対応
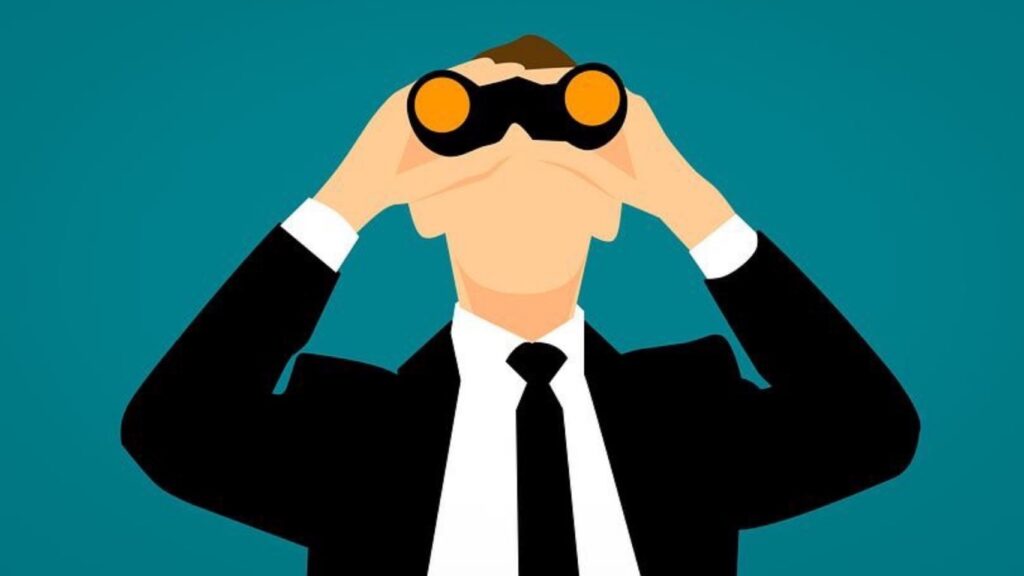
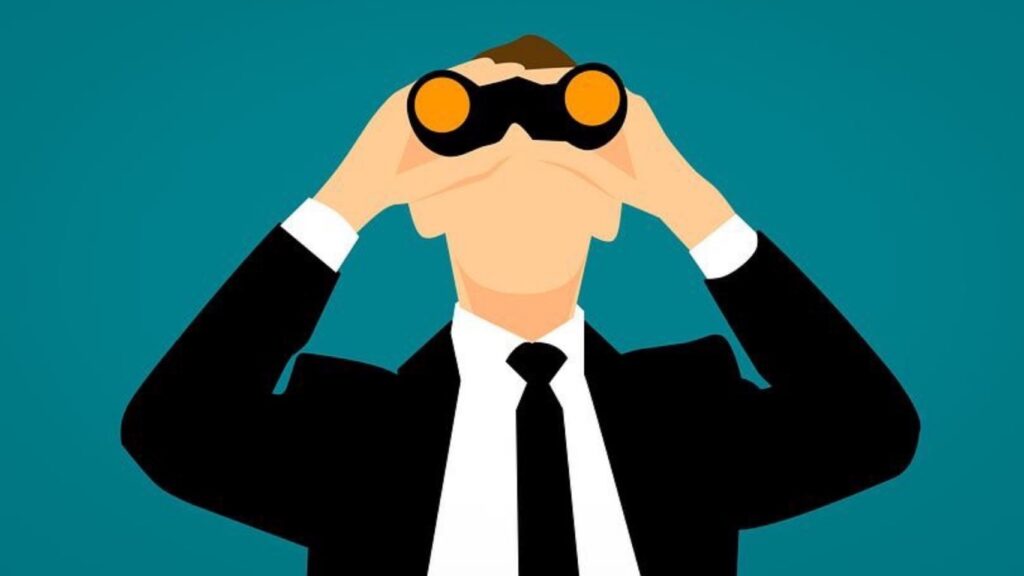
工場にトラブルはつきものです。
品質不具合、設備故障、労災など。
忙しい時に限って携帯がよく鳴る。それが生産技術です。
品質保証や保全などの他部署と連携を取りながら
柔軟に解決することが必要となりますので
良好な人間関係の構築が大切です。
メーカー生産技術に必要な知識・資格
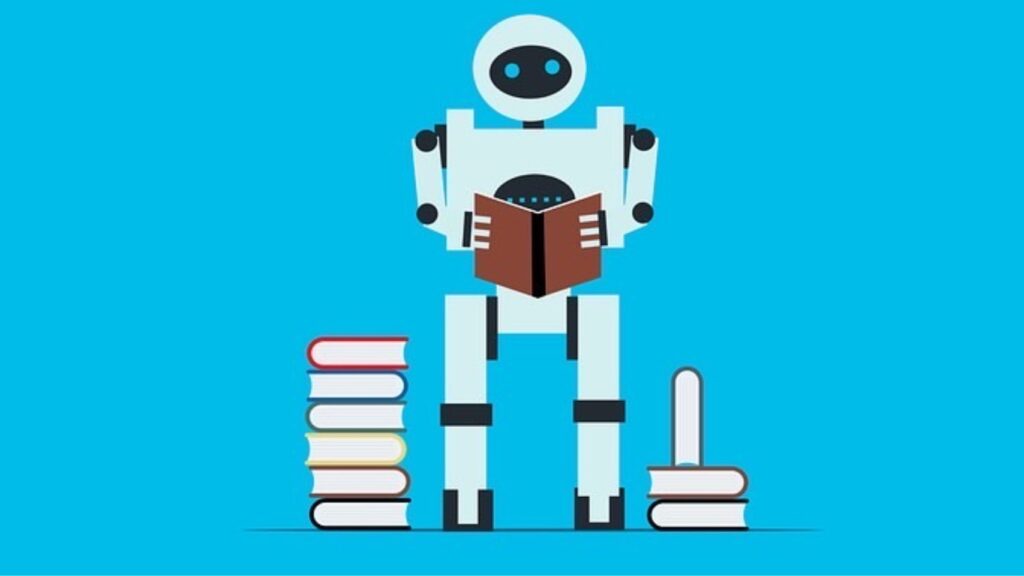
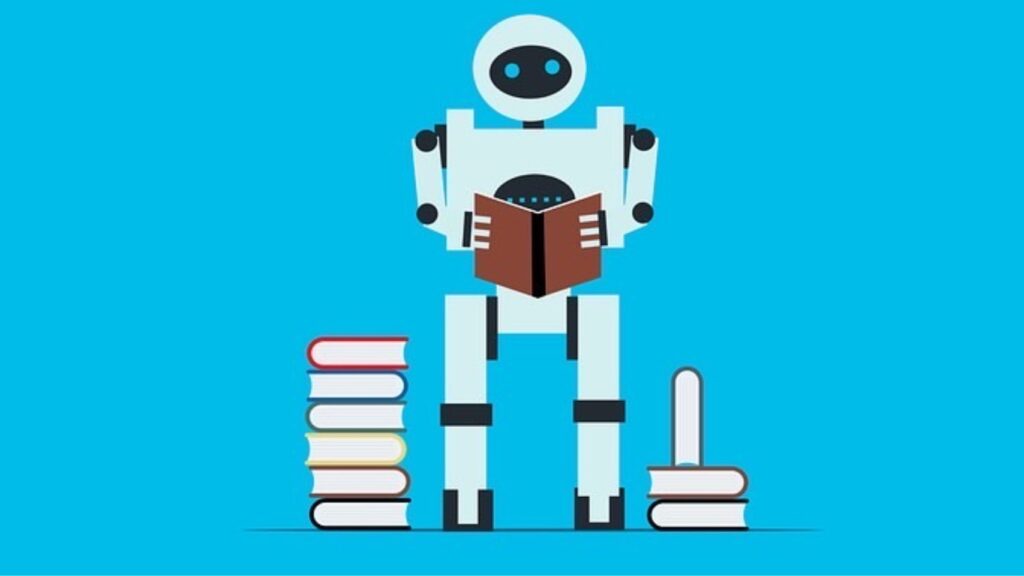
業務の中であったら良いと思える知識と資格の紹介です。
ちなみに私が保有していて
業務内の役に立ったと感じた資格は
・製図関連の国家試験2級
・QC検定3級
です。
資格で表すのは難しいので「知識」の表現で箇条書きすると
・図面関連
→ 製品図面はもちろん、設備図面もある程度の読解力は必要となります。
あわよくば電気図面まで読解したいです。
・設備関連
→「安全」の知識はもちろん
油圧・空圧やセンサーの知識があると特注で設備を導入する際に役立ちます。
・Excel関連
→資料作成やデータまとめの際に必ずと言っていいほど使用しますので幅広い関数の知識やあまり知られていない便利な機能の知識があると業務効率が上がります。
・QC(品質)関連
→ ライン立上げ時の品質確認の時にQCの知識は必須となります。
・語学
→特に英語です。苦手だと海外案件の際に苦労することがあるかもしれません。
この中でも英語力は昇格・昇進の条件のひとつとして採用されていることがあり
社員の英語力の見極めにTOEICの点数を採用する企業が増えてきています。
仕事はできるのにTOEICがネックで昇格できない…
なんてこともある時代です。
それくらい語学力が重宝される時代なんですね。
メーカー生産技術のつらいこと
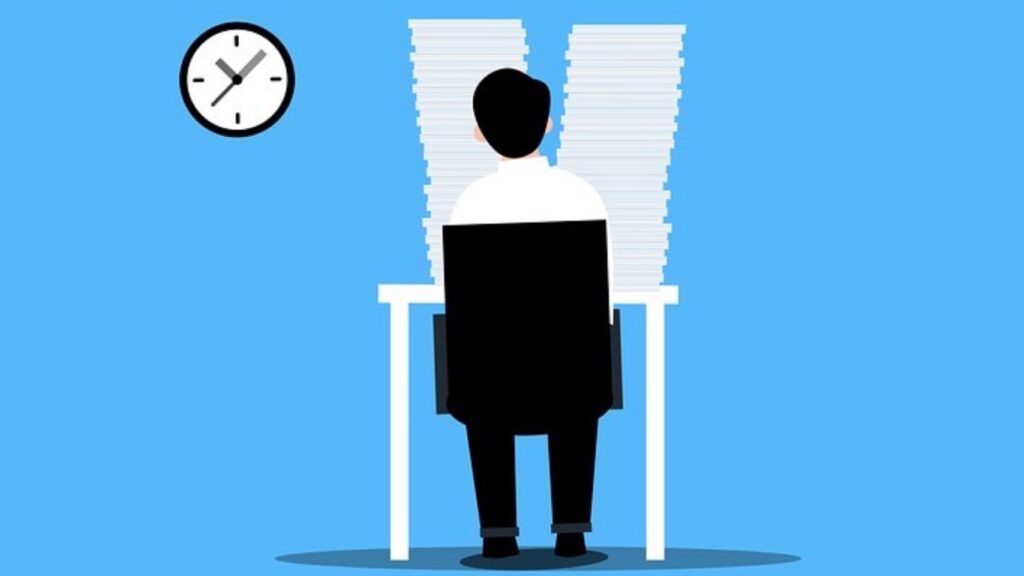
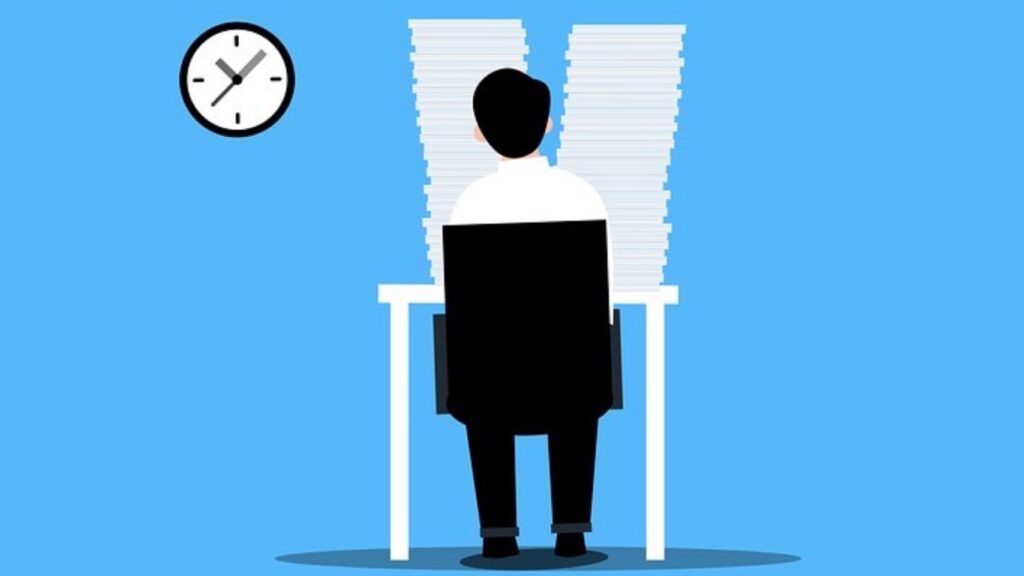
「休日出勤&残業」
生産技術ってこのイメージがあるんじゃないでしょうか。
休日出勤
実際にあります。
他の部署に比べたら多いと思います。
しかし
やみくもに休日に出勤しているわけではないです。
検証1つにしても量産の設備で確認が必要な時
設備が止まっていないと確認できないですよね。
では問題
Q.設備が止まっている日はいつでしょう
→休日!
というわけで
やむおえず休日に出勤して検証などを行っています。
残業
残業をせざるおえないことが多いです。
理由は「納期」です。
ライン立上げは決して自分のペースではできないです。
案件の最初の段階で
生産管理にガチガチに日程組まれます(笑)
基本的にこの最初に決まった日程からは
延びないものとして業務に取り組みますが
これがとても大変です。
1番の問題は「想定外のトラブル」です。
私の経験だと設備トラブルが挙げられます。
設備がいつ直るかなんて
正直何年やっても分からないですよ(笑)
そんな終わりがはっきりしていない
設備の復帰作業を決められた納期までにと考えると
どうしても休日出勤や残業が多くなってしまいます。
・トラブルが多く中々予定通りに進まないが
納期は基本的にSTAY(延びない)
・業務の終わりがはっきり見えていなくても
納期は固定されている。
業務の終わりがはっきり見えないライン立上げをしながら
既設設備に不具合があれば対応しなければいけません。
「この案件…納期間に合わないかも…」
このプレッシャーがあるのが生産技術の苦しいところです。
メーカー生産技術に向いている人
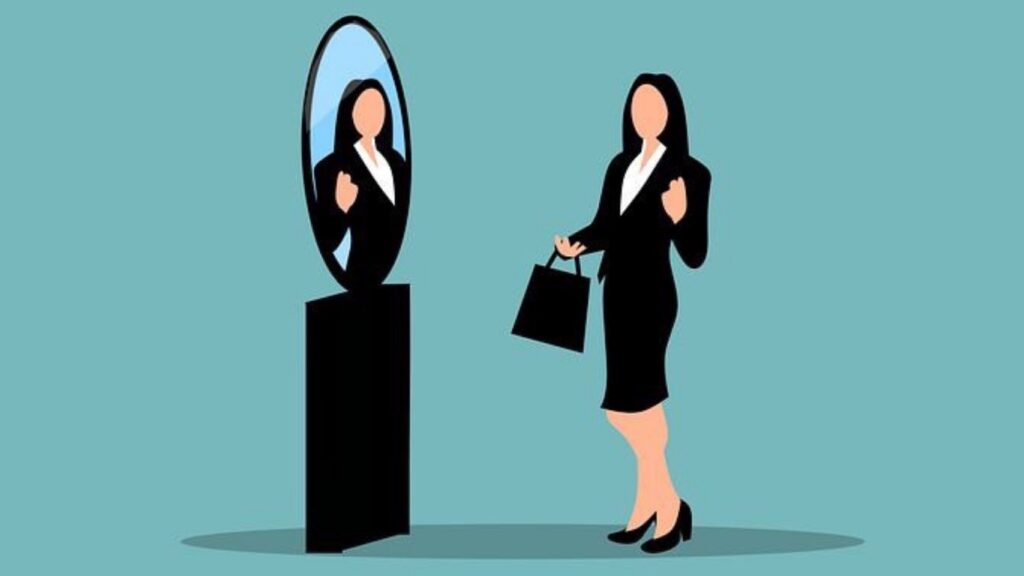
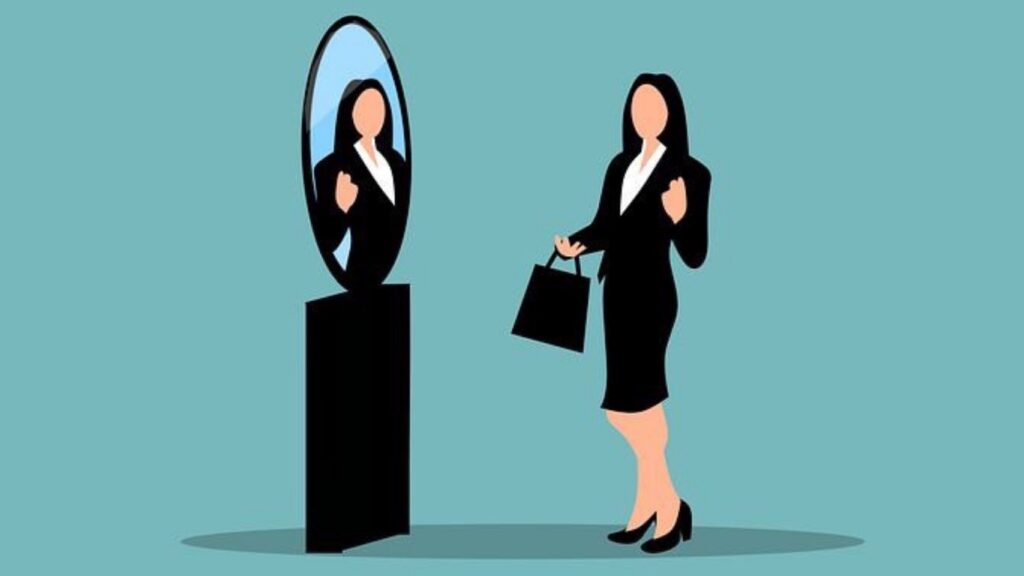
実際に業務を行っていく中で
こんな人が生産技術に向いている人だと思いました。
コミュニケーション能力が高い
どの職種に関しても
コミュニケーション能力は必要です。
報告などでアウトプットが上手くできるかどうかは
「出世」にも関わりますし
他部署やメーカー・商社に遠慮なく意見が言えると
業務を効率よく進めやすくなります。
現場とのコミュニケーションは
設備の借用やデータ取得のお手伝いなどのお願いが
楽にできる関係の構築ができると◎です。
発送力が豊か
生産技術は答えのない仕事が多いです。
そんな時に必要なのが「発想力」です。
設備レイアウト検討時に
設備の設置向きを変更してなんとかエリア内に収めたり
カタログ機にない
完全な一品ものをゼロから発注したりと
発想力の豊かさが大事な場面が多いです。
要所で几帳面
「要所で几帳面…」
これはまた難しい(笑)
自分が結構大雑把な性格のせいで
ミスをしてしまうことが多いので
「几帳面さ」が必要なことは重々承知していますが
業務量が多い分
内容によってはある程度
大雑把に業務をさばいていくことも重要です。
生産技術には
要領よく優先度が「低」の業務をさらっと50%程度で
さばく大雑把さは必要だと思います。
几帳面だと「確実に」の精神で
すべての業務に100%の力で取り組むと思いますが
疲れちゃいますよ(笑)
基本的な性格は大雑把だけども「要所で几帳面」な人が職種関係なく1番効率が良い方だと思うので目指しましょう(笑)
では問題の「生産技術」で几帳面になるべきポイントですが
①「検証」
検証の条件に漏れがあると
大きな痛手になる可能性があります。
※材料が不足など
そのため
入念な確認でミスを起こさないような心掛けが必要です。
また
量産設備を借用して検証を行う場合は
検証後の条件戻しは必須です。
条件戻しを忘れると
返却後に違う条件で製品が生産されることになるので
大量の不良をだしてしまう大事件につながる可能性があります。
②「データまとめ・報告」
検証結果を図やグラフ・表を使ってまとめますが
これも見やすい資料を意識して取り組む必要があります。
上位報告があるものは尚更です。
例えば
上位に「A」と「B」の検証結果について2人が報告しているとします。
大雑把くんの報告
「A」のが「B」より重かったです。
両方とも規格内でしたよ。
几帳面くんの報告
「A」のが「B」より10g重かったです。
規格:30±15gに対して
「A」は35g 「B」は25gでしたので
規格内で推移はしています。
重さに差が出た要因としては
製品外観は確認したところ問題がなかったため
材料切り出し装置のバラつきが考えられます。
本日中に装置内の履歴を確認して再度報告します。
どっちの報告が良いですか?
私が上司なら
大雑把くんには数値まとめて再報告って言いますね。
←なぜか?
「規格内」だったと言っているが極端な話
もし 規格:30±15g に対して44.9gだった場合は
n増しすると規格外になる懸念があるからです。
上記の2人の報告、何が違うのか?
→それは具体的な数値を提示しているかどうかです。
エビデンス(証拠・根拠)は数値で示す
これはとても大事なことです。
要は
「けっこう大きい」など
定量的な表現をやめようということです。
具体的にどれくらいなのかを%などの数値で表す。
これが重要です。
ちなみに私はコミュニケーション能力と発想力は並。
どちらかと言えば大雑把な性格ですが
何とか「生産技術」の業務に従事していますので
「やる気と根性」があれば誰でもできると思います!(笑)
忙しいですが
その分「やりがい」を感じることも多いですので
仕事に「やりがい」を求める人にもおすすめですね。
まとめ
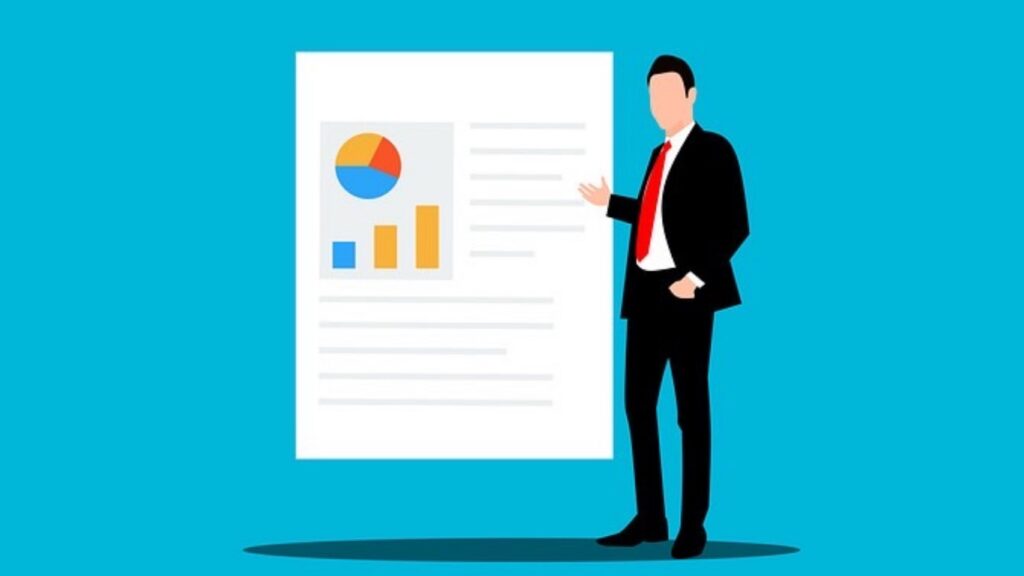
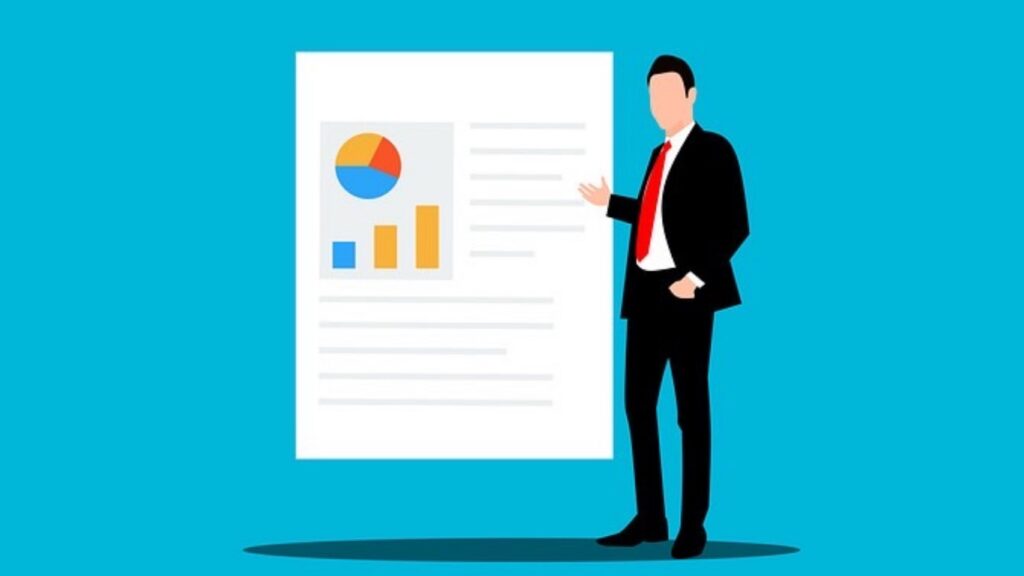
いかがでしたでしょうか。
今回は
「メーカー生産技術の仕事内容。向いている人」
について解説しました。
まとめです。
・メーカー生産技術には大きく分けて
工法開発/生産準備/工程改善がある
・メーカー生産技術には図面・設備・品質など
多様な知識が必要
・メーカー生産技術は納期のプレッシャーがつらい
・メーカー生産技術に向いている人は
・コミュニケーション能力が高い
・発想力が豊か
・要所で几帳面
本記事で
「生産技術」の仕事内容について
理解が深まったかと思います。
「生産技術の業務量多すぎるよ!」と感じたと思いますが
分担してチームで仕事を進めていくのが
生産技術の良いところです。
多くの業務をひとりで行うわけではないので
これから「生産技術」として働く人は安心してください。
- 仕事にやりがいを感じたい
- 発想力を最大限に生かしたい。
など「生産技術」に興味のある人は
ぜひ、挑戦してみてください!
新卒/中途採用ともに求人は多数ありますので!
みなさんが
理想のキャリアを描けること願っています。
それでは、このへんで。
コメント